What is the key difference between Prototype, Prelaunch and Production Control Plan?
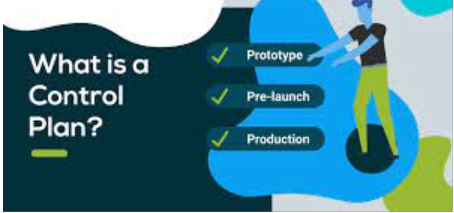
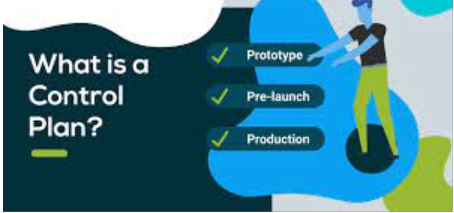
The difference between music and noise is in what musician does with the sound: Jean-Michel Jarre
Introduction
In India, when a child is born, there is a tradition for thousands of years, to prepare a horoscope (Janampatri). It not only tells information (Karmas) about their past but also about the prediction in this birth too. At present times, we have Social Security Number or Aadhar Card (in India) which gives complete information about a person. Very recently, Google has more personal information about you than even your spouse. Although the technologies are different, it serves the same purpose of providing information.
Objective
As per APQP manual (Advance Product Quality Planning- AIAG) in different stages of the product development, there are 3 different types of control plan which are prepared so that at each stage, the product quality can be ensured and customer requirements can be fulfilled (as per PPAP-Production Part Approval Process Manual-AIAG). By understanding these 3 types of control plans (Prototype, Prelaunch, Production) and their key differences, the organization can fulfill the needs and expectations of their customers and relevant interested parties.
Definitions
Control plan: Documented description of the systems and processes required for controlling the manufacturing of the product
Prototype: A description of the dimensional measurement, material, and performance tests occurring during prototype buildup to assess an experimental or developmental formulation.
Prelaunch: A description of the dimensional measurements, material, and performance tests affecting special characteristics that will occur during product scale-up and before normal production.
Production: A comprehensive documentation of product/process characteristics, process controls affecting special characteristics, tests, and measurement systems occurring during normal production.
Detailed Information
Control Plan is the backbone for the Manufacturing process. It is considered to be a LIVE document. There are more than 20 clauses of the IATF 16949 Standard wherein it is referenced. Also, many IATF subscribing OEMs (GM, Volkswagen, FCA) specify their additional requirements in their supplier manual.
Although the APQP manual (2nd Edition) has specified a template for different types of Control Plan, the organization can decide its template (or as per customer specific requirement) but ensuring that all the contents as specified in IATF 16949 Standard (Annexure A Page 54) are specified.
Following are some of the key Difference between Prototype, Prelaunch, and Production Control Plan:
S.No. | Prototype | Prelaunch | Production |
1 | Samples may be made with temporary tooling | Pilot Lot made with tooling which should be used in mass production | Mass production is done with tooling approved during the prelaunch stage and approved by the customer |
2 | An output of DFMEA (APQP Phase 2) | An output of PFMEA (APQP Phase 3) | An output of PFMEA (APQP Phase 4) |
3 | The purpose is to prepare few samples (2 to 5 numbers) | The purpose is manufacturing a lot as per customer requirement (8-hour production/300 pieces) | The purpose is to do mass production |
4 | The process sequence will not be complete and may change later | The process sequence will be fixed but may change after trial production | The process sequence will be freeze and followed during mass production |
5 | The importance of Tolerances is negligible | The role of Tolerances is important to ensure fitment and function as per customer requirement | |
6 | No special characteristic defined | The special characteristic will be defined | |
7 | Sample Size is 100% | Considering a pilot lot of 300 or more, the Sample size will be high (example: 50) | It may be 2 or 5 pieces considering the criticality of the process/product |
8 | Inspection frequency will be 100% | Inspection frequency will be high like every 10th piece (assuming manufacturing a pilot lot of 300 or more) | Maybe every 2 hours/4 hours considering the criticality of the process/product |
9 | The Evaluation method like gauges, measuring instrument, etc. may be temporary | The evaluation method will be finalized and may remain the same | The evaluation method like gauges, measuring instrument, etc. will be Final |
10 | No statistical study is planned | The statistical study is planned to check how the process is performing | The statistical study is planned to verify the stability of the process (Xbar/R Chart, p/np, c/u, etc.)
|
11 | No Poka-Yoke implemented at this stage | Poka-Yoke is implemented and is verified for their effectiveness and any further improvement | Poka-Yoke is finalized and implemented |
12 |
No need for any Reaction plan | A reaction plan will be prepared but can modify after trial production | The reaction plan will be finalized and followed |
Present Challenges
- Control Plan is considered to be a LIVE document but is it true? In many organizations, Control Plan is not reviewed even after 5 years!!
- How often we check the accuracy and linkage between Drawing, Customer Requirements, Customer Specific Requirements, DFMEA, Process Flow Chart, PFMEA, and Work Instruction?
- How often changes are made in the prelaunch control plan apart from changing the tick mark from the box to ‘Production?’
- How often the organizations are clear about the key differences between the 3 types of Control plans?
References:
APQP Manual 2nd Edition (AIAG)
PPAP Manual 4th Edition (AIAG)
IATF 16949: 2016
iatfglobaloversight.org
Industry Experts
This is the 115th article of this Quality Management series. Every weekend, you will find useful information that will make your Management System journey Productive. Please share it with your colleagues too.
Your genuine feedback and response are extremely valuable. Please suggest topics for the coming weeks.
Recent Comments