APQP: New Product Development: Process Design (Phase 3)
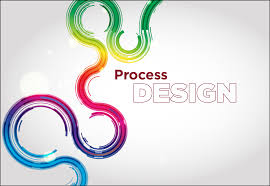
APQP: New Product Development: Process Design (Phase 3)
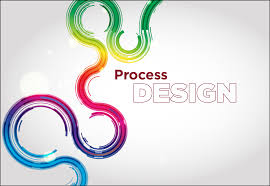
“Good design is like a refrigerator—when it works, no one notices, but when it doesn’t, its sure stinks.” –Irene Au
Introduction
When a voyager decided to travel, the first thing is to have a map (design) and the next important thing is to plan ‘how to reach the desired destination, what preparation needs to be done like the type of ship, the number of people, type of equipment etc.’ Once the required preparation is done, the actual journey starts.
Something similar happens in process design. Wherein based on the product design output, the process to achieve it is planned and executed.
Objective
As per the process approach, the output of one process becomes output for another process. Something similar is expected in this phase too wherein the key and relevant output of product design phase becomes important input for the process design phase. The multidisciplinary team should analyse and understand the inputs and convert them into useful output for the next process. As in this phase product/service becomes tangible, it will also reflect the performance of previous phases. The manufacturing process should assure that needs and expectation of the relevant interested parties and customer requirements are met.
Definitions
As per IATF 16949, clause 3.0, following are some of the key definitions related to the design process
Advanced product quality planning (APQP): product quality planning process that supports the development of a product or service that will satisfy customer requirements; APQP serves as a guide in the development process and also a standard way to share results between organizations and their customers; APQP covers design robustness, design testing and specification compliance, production process design, quality inspection standards, process capability, production capacity, product packaging, product testing and operator training plan, among other items.
Special characteristic: classification of a product characteristic or manufacturing process parameter that can affect safety or compliance with regulations, fit, function, performance, requirements or subsequent processing of the product.
Trade-off process: methodology of developing and using trade-off curves for products and their performance characteristics that establish the customer, technical, and economic relationship between design alternatives.
Customer Specific Requirements (CSR) of IATF subscribing OEM
Following are their key requirements
Daimler:
Special Characteristics: MBST 13/18, section 5, paragraph 3 + 7
PPAP: MBST 13/18 complete Production Process and Product Approval (PPA)
Design and development changes – supplemental: MBST 13/18, section 4 MBST 13/18, section 5
FCA:
Design & Development: SQ.00010 Advance Quality Planning (AQP) and PPAP
Embedded Software: assessment of software process capability/maturity: as per CS.00187
GM:
PPAP: GM 1927-03 Quality SOR
Detailed Information
As per IATF 16949, Clause 8.3 and APQP manual (Advance Product Quality Planning- 2nd edition, July 2008), there are 5 key phases. They are
- Plan and define the program
- Product design and development verification
- Process design and development verification
- Product and process validation
- Feedback, assessment and corrective action
As per APQP manual, 2nd edition, following are some of the key inputs (which are output from Product Design Phase)
- Engineering drawing
- Engineering Specifications
- Material Specifications
- Design Failure Modes & Effect Analysis (DFMEA)
- Design for Manufacturability and Assembly (DFM, DFA)
- Prototype Control Plan
- New equipment, tooling and facilities requirement
- Special product and process characteristics
- Gauges / Test Equipment requirements
- Reliability study
- Service diagnostic guidelines and repair and serviceability instructions
- Service parts requirement
- Design Verification
- Design Review
- Drawing and specification changes
- Team Feasibility commitment and Management support
Based on the above inputs, the following are the possible outputs from this phase
Preparation of Documentation:
- Specification and Drawing: One of the key outputs of customer requirement and control plan will be the specifications for product and process. It can be related to fit, function and measurement.
Based on the product drawing, during this phase, sub-assembly drawing can be prepared where needed. Example: In Fabrication process (Press shop), there are different stages like blanking, drawing, trimming etc. To understand the product specification at each stage, drawing of the subassemblies can be prepared to review and measure the dimension at each stage.
- Process flow chart: This is the first document which helps to visualize the entire process from beginning to end (bird’s view). During team feasibility study wherein existing capacity and capability is reviewed, the process flow chart plays an important role. It is a schematic diagram which reflects the proposed and existing flow of the processes from beginning till end. It helps the CFT (cross-functional team) to identify the key processes and possible sources of variation in 4M (man, machine, material and method).
- Floor plan layout: Based on the process flow chart, floor plan layout can be prepared. It is a pictorial view of the entire proposed process. It contains details about the flow of material from the incoming stage to despatch of finished goods. It can cover minute details like the location of in-process inspection, material storage, repair, rework & segregation location etc. The overall intent is to visualize and ensure that material flow is synchronous, the utilization of floor space is minimal, the movement of operators is systematic so the lean management principles can be effectively implemented.
- Characteristics matrix: The main objective of the characteristic matrix is to define the relationship between different processes in the manufacturing like machining, drilling etc. and different process/product parameters like outer diameter, flatness etc. By identifying the relationship between manufacturing processes and process/product characteristics, the understanding of the entire processes enhances and becomes useful for PFMEA and Control plan preparation.
- Identification of error proofing: In present times, the impact of rejection and delay is very high. To avoid any such losses, the organization can plan error proofing (poka-yoke) in different stages of the process. The criteria can be special characteristic related to product quality, safety requirement, repeated customer complaint, high rejection etc. Example: To meet Euro 6 emission norms, the fool proofing can be installed at the final inspection so that any vehicle who is not meeting the criteria cannot be approved and move further.
- Process Failure Mode and Effect Analysis (PFMEA): As per AIAG/VDA manual or as per customer specified manual, an organization can prepare PFMEA by using cross-functional team (having process owners from relevant processes) before starting the production to understand the possible failures so that suitable actions (detection/prevention) can be planned. PFMEA is a live document which can be reviewed
- at a certain periodic frequency
- whenever there is any change in the process
- customer complaint
- rejection (internal/external)
- Customer requirement
- Pre-launch Control Plan: After prototype sampling by using prototype control plan and before mass production, an organization can prepare pre-launch control to define dimension, functional and material test. The main objective of the pre-launch control plan is to identify and control the possible non-conformities before mass production. Some of the key difference between prelaunch and mass production control plan includes
- Frequent inspections
- Bigger sample size
- Detailed statistical controls and evaluations
- Verification of effectiveness of fool proofing
- Process approval acceptance criteria: To achieve product requirement, the process has to be designed wherein for different stages there can be process parameters which need to be monitored. Each process parameter will have its acceptance criteria. Example: In the moulding process, Temperature (180 degrees) can be a process parameter. The tolerance of 10 degrees will be its acceptance criteria. Similarly, a limit sample for visual inspection of a moulded component can be an acceptance criterion.
- Work Instructions: Work instruction intends to guide the concerned operator, supervisor and inspector to work as per certain guidelines. The work instruction includes the requirement of safety for the operator. work instruction should be in a language which is understood by the user and is easily accessible (does not mean that it should always be displayed in front of the operator). The work instruction is an output of
- Process flow chart
- PFMEA
- Control Plan
- Characteristics matrix
- Engineering drawing
- Customer requirements
- Material specifications
- Floor plan layout
- Packaging standards: It is said that the ‘success of the organization depends on its weakest link.’ The packaging standard will be an output of the customer requirement and the organizations’ internal packaging standard. Wherever the customer does not provide packaging standard, the organization can define their standard but needs to take approval from the customer before dispatch. The packaging quality intends to ensure the integrity of the product until the time it reaches the actual user. Moreover, the packaging standard should also ensure easy handling at the organisation as well as the customer end. Example: At many customers location, the size of the storage location is fixed and material handling equipment including manpower/robot has limitation in carrying certain weight/size.
Output of Documentation
- Measurement System Analysis plan (MSA): As per AIAG (Automotive Industry Action Group) manual 4th edition or customer-specific requirement, an organization can make a plan for all the measuring instruments, gauges, test equipment etc. which are referenced in the control plan. The intent is to verify that error due to measurement is limited and can be measured. The MSA study includes measurement of repeatability, reproducibility, linearity etc.
- Preliminary Process Capability Study plan: As per AIAG manual 2nd edition or customer-specific requirement, an organization can make a plan for all the special characteristics (Critical, Major) which may impact the process and product characteristics. Capability study is one of the key outputs of FMEA and customer-specific requirement. The study intends to verify that capability of the process in meeting the product requirements. Some of the popular capability studies include Xbar / R Chart, p/np, c/u etc.
- Tooling and Equipment for production: Based on the product drawing, customer specifications and DFMEA, the organization have to manufacture or procure the tooling and equipment needed for their manufacturing process. The tooling can be related to moulded components, sheet metal components or anything similar to that. The equipment is procured from relevant interested parties for production, quality, inspection and testing process. The purchase process (SCM-Supply chain management) has an important role in the procurement of tooling and equipment.
- Maintenance plan: One of the key outputs of product and process FMEA is the performance criteria for the maintenance of machines like planning for predictive and preventive maintenance. Based on the criticality of the machines, identification of the critical machine and their related spare parts can be done in this phase.
- Data for quality, reliability, maintainability and measurability: Based on the customer requirement and product design, there can be few inputs to the process design process like a target for process capability and rejection, warranty, delivery performance, variation in measurement system etc. To monitor the performance of these key objectives, the data can be collected at different stages of the production through SPC study (Statistical Process Capability-Mean & Range), MSA Study (Measurement System Analysis-Repeatability, Reproducibility, Linearity), internal rejection, machine breakdown, OEE (Overall Equipment Effectiveness), customer rejection etc.
- Methods of rapid detection, feedback, and correction of product/manufacturing process nonconformities: The expectation of the customer and end-user is increasing rapidly. To achieve customer expectations, internal processes should be designed in such a way that abnormalities can be identified at an early stage, it can be escalated to the appropriate person and desired actions can be taken to correct it. Example: In a CNC machine, if any electric motor behaves abnormally like taking more load/vibration / more noise than usual, than through condition-based monitoring process, it can be identified before the motor gets under breakdown. The communication can be shared with relevant maintenance personnel so that the desired action can be taken to avoid any further losses. Similarly, fool proofing is another method of rapid detection.
Internal communication mechanism can be established so that real-time communication can be shared with the concerned process owner like maintenance process. Example: Buzzer / online performance of the machine is displayed at the maintenance office/use of social media like Whatsapp is done for quick communication.
- Capacity analysis: Based on the customer requirement & capacity agreement with the customer in the initial phase, now the actual performance of the capacity has to be verified. The intent is to check and verify the effectiveness of process flow, floor plan layout, the competence of operator, procured equipment and inspection method. The Run-at-rate verification will give the actual performance of the designed process for product quantity and quality. Based on the results, wherever needed, the desired action can be planned and taken to reach the desired level.
- Product and process quality system review: During this phase, the review of the existing manufacturing facility by the cross-functional team will help the organization to identify the gaps between customer expectations and existing facility. The key changes can be updated in the control plan so that during the manufacturing phase, all the requirements can adhere to. The kind of checklist to be used for this review will vary based on the customer and their product/process requirements.
- Management Support: The key intent of team feasibility commitment is that the CFT will review and analyse all the process design related inputs so that organization is confident that they can manufacture, test, package and despatch the desired quality product to the customer on time. During this phase, if CFT identifies few areas which may not be possible to implement, they can escalate to top management for their intervention and support.
Benefits to Organization:
- Voice of the customer can be met
- Relationship with the customer can be improved
- The cost of production can be managed effectively
- Competency of the employees can get enhanced
Present Challenges:
- How often the voice of the customer is understood properly and implemented in process design?
- How often the cross-functional team works collectively and effectively?
- How often the key inputs related to quality, cost and delivery are either achieved or monitored after the process design phase?
- How often the gap analysis of the competency of the personnel working in the process design phase is identified and actions are taken to improve it?
References:
ISO 9000: 2015
ISO 9001: 2015
IATF 16949: 2016
APQP 2nd Edition
This is the 77th article of this Quality Management series. Every weekend, you will find useful information that will make your Management System journey Productive. Please share it with your colleagues too.
Your genuine feedback and response are extremely valuable. Please suggest topics for the coming weeks.
sir it is necessary to add topics like “MSA study plan” and “SPC study plan” in Phase 3 of APQP?
Dear Manoj, Thanks for your query. If there are special characteristics or there is a requirement of the customer, Phase 3 is the appropriate time to plan SPC and MSA.