Maintenance Process
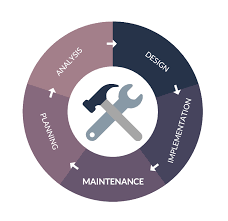
Maintenance Process
“If I had six hours to chop down a tree, I’d spend the first four hours sharpening the axe.”: Abraham Lincoln
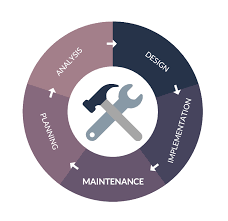
When a person goes to the gym, the intent is not to repair the muscles but to make them stronger. When we do meditation, we are not intending to eliminate any illness but to strengthen our mind to face any challenge. When we send our automobile to a service station for annual maintenance, the intent is to verify its potency and how it can be enhanced. Similarly, the purpose of the maintenance process is not to repair any machine or utility but to keep them in healthy & working condition.
The key objective of the maintenance process is to establish a robust management system so that desired quality and delivery performance of the products and services can be ensured by having maximum equipment effectiveness through employee involvement and adequate backup of resources like manpower, spare parts etc. The expectation of this process is to keep the entire facility in healthy condition although in case any equipment is under breakdown, its repair is also the responsibility of this process.
Over a period of time, with the rise of the Industrial Internet of Things (IIoT), some of the organizations have started using intelligent maintenance software to collect data and integrate with connected devices to get smarter about manufacturing.
With TPM, the concept has changed from ‘I operate, you maintain’ to ‘My Machine Concept.’
As per IATF 16949 clause 3.0, following are some of the key definitions
Periodic overhaul: Maintenance methodology to prevent a major unplanned breakdown where, based on fault or interruption history, a piece of equipment, or subsystem of the equipment is proactively taken out of service and disassembled, repaired, parts replaced, reassembled, and then returned to service.
Predictive maintenance: An approach and set of techniques to evaluate the condition of in-service equipment by performing periodic or continuous monitoring of equipment conditions, in order to predict when maintenance should be performed.
Preventive maintenance: Planned activities at regular intervals (time-based, Periodic inspection, and overhaul) to eliminate causes of equipment failure and unscheduled interruptions to production, as an output of the manufacturing process design.
Total productive maintenance: A system of maintaining and improving the integrity of production and quality systems through machines, equipment, processes, and employees that add value to the organization.
As per ISO 9001 and IATF 16949, Clause 8.5.1.5, there are 3 key maintenance activities. They are
- Preventive Maintenance
- Predictive Maintenance
- Periodic Overhaul
- Preventive Maintenance (Scheduled/Proactive): It is planned maintenance which is conducted based on different parameters like criticality of the machine, number of breakdowns, availability of spare parts etc. Based on the above analysis, the organization can have plan frequency for conducting preventive maintenance. Moreover, preventive maintenance for each machine can also be further bifurcated periodically (daily / weekly/fortnightly / monthly / yearly) based on machine behaviour. The goal of this approach is to extend the useful life of an asset and prevent breakdowns from occurring.
- Predictive Maintenance: It aims to predict failures before they happen so maintenance can occur at just the right time. Depending upon criticality and availability of technology, an organization can use data from visual inspection, machine sensors and smart technology to alert the maintenance team when a piece of equipment is at risk of failing. For example, a sensor may use vibration analysis to alert the maintenance team that equipment is at risk of failing, at which point it will be taken offline, inspected, and repaired accordingly.
- Periodic overhaul: It is a rework of manufacturing tooling and equipment needed when regular maintenance activities are no longer enough to keep the tooling and equipment in a condition where it can continue to make a product to specification, as detected using Mean Time To Repairs (MTTR) or other similar metrics (MTBF). It is a special requirement which can be followed by manufacturing industries wherein due to regular breakdown or high cost of production, the organization has to stop a machine for a longer period and plan detailed repair. As this process can consume a few weeks or months to overhaul the machine, the organization may have to build up advance inventory. If needed, the customer also needs to be intimated and their approval may be needed if the machine is approved by the customer. In such cases, there may be a need for PPAP approval for a different machine. As overhauling will result in the consumption of manpower, time, material etc. capital expenditure also may be needed, depending upon the number of machines and expenses involved.
To accomplish the above 3 key activities, following support actions are needed to make it effective. They are
Identification of key process equipment: In any manufacturing process, there may be n number of machines. Depending upon the importance of the machines to fulfil customer demand, an organization can define key machines which need more attention than others. The organization can categorise them based on its
- Criticality
- repeated breakdowns
- age of machine
- backup plan
- usage
- cost of maintenance
- desired infrastructure
- required time
- its effectiveness.
The key output is to produce good quality product as per customer requirements for performance and delivery time.
The bottom line is that there is “no one size fits all” approach to maintenance. To develop a maintenance strategy, the organization has to evaluate and weigh the unique benefits and shortcomings of each strategy, depending on what assets organization is working with, what stage of the reliability journey the organization is at, and the impact of downtime at the manufacturing facility.
Availability of replacement parts: For ensuring uninterrupted production and supporting the maintenance process, availability of replacement parts for the key machines is pertinent. The organization can categorise the inventory of replacement parts based on the
- the criticality of the machine
- its lead time for procurement
- its availability
- cost of procurement
- other factors relevant to the organization.
The minimum and maximum inventory level can be defined and maintained.
Provision of resource: For ensuring sound health of the machines and utilities (compressor, Generator, ETP, STP, cooling tower, LPG/CNG etc.), the organization has to provide adequate resources like
- competent manpower
- spare parts
- infrastructure
- annual maintenance contract
- adequate time for maintenance
- contract with the manufacturer.
Example: For the moulding machine, the quality of hydraulic oil has to be checked periodically, the organization may purchase the machine to reduce dependence on the external body.
Packaging and preservation: For machines, tooling and gauging, desired protection is important so that they can perform to the desired level. Some of the key preservation includes
- periodic greasing of machines
- applying rust preventive oil
- covering tooling and gauges with plastic cover, when not in use.
Customer-specific requirements: Some of the customers do have their own specific requirement related to the maintenance process. Although no IATF subscribing OEM has specified any requirement related to TPM so far. The intent is to ensure that organization have an effective system to ensure that their machines are in healthy condition.
Maintenance objectives: The success of the organization for timely delivery and quality of the product and services depend upon meeting the key maintenance objectives. Some of them can be
- OEE (Overall Equipment Effectiveness)
- MTBF (Mean Time Between Failure)
- MTTR (Mean Time to Repair)
- Planned preventive maintenance adherence
- Planned predictive maintenance adherence
- Minimum/Maximum inventory level for critical spare parts
- Reduction in breakdown hours
The maintenance objectives can be key inputs for the top management review. The intent is to ensure the management is aware of the existing health of the machines and possible actions needed based on the trend charts like overhauling of the machine etc.
Review of maintenance plan and objectives: Once the objectives are defined, the organization can plan to periodically review the effectiveness of maintenance objectives. The achievement of these objectives is key to the achievement of production and desired quality. Apart from objectives, plan for preventive and predictive maintenance of key machines and desired inventory levels of the critical spare parts can also be reviewed regularly. Wherever target and plans are not met, a systematic analysis and action plan can be prepared by using the CFT (cross-functional team) approach so that their effectiveness can be assured.
Key benefits of the effective maintenance process
- Decreased equipment downtime and repair
- Increased equipment life expectancy
- Reduced overtime cost
- Improved safety and work conditions
Possible Challenges:
- In the 21st century, we are still operating with the concept ‘I work, you maintain!’ When it will change?
- How often a predictive maintenance plan is prepared and implemented effectively?
- How often maintenance process identifies the customer-specific requirements (CSR)?
- How often critical spare parts are identified and available for critical machines?
References:
ISO 9000: 2015
ISO 9001: 2015
ISO 9004: 2018
IATF 16949: 2016
This is the 68th article of this Quality Management series. Every weekend, you will find useful information that will make your Management System journey Productive. Please share it with your colleagues too.
Your genuine feedback and response are extremely valuable. Please suggest topics for the coming weeks.
Recent Comments