What is the key difference between Cp and Cpk?
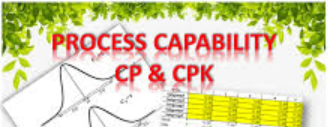
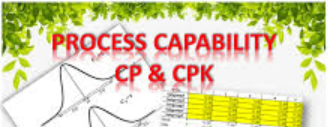
There is a big difference between giving up and knowing when enough is enough: Unknown
Introduction
There is a subtle but key difference between belief and trust. When we have a belief in someone like God, it means we know something about it but we may not have practised it or realized it. But, when we trust someone like God, it means we not only have experienced it but also have faith in it.
Objective
To prosper in today’s economic environment, it is important to continually improve our processes. We must continue to seek efficient methods of improving our products and services to enhance their value.
To accomplish this, understanding the processes, their variation (common and special cause), reasons why it is happening and its statistical interpretation is pertinent. To understand more about it, clarity about Cp and Cpk is necessary.
Definitions:
Process Capability: It is determined by the variation that comes from the common causes. It generally represents the best performance of the process itself. This is demonstrated when the process is being operated in a state of statistical control regardless of the specification.
Cp-Process Capability: A simple and straightforward indicator of process capability.
Cpk-Process Capability Index: Adjustment of Cp for the effect of non-centred distribution.
Detailed Information
Dr Walter Shewhart developed the first control chart in the 1920s to describe common and special causes. The key objective of implementing statistical techniques is to
- Improve quality
- Increase productivity
- Reduce cost
To achieve the above objective, the intent should not be to implement statistical tools on the products only but on the processes, which are creating those products.
There are 2 key needs for process controls through statistical techniques
- Detection (tolerates waste)
- Prevention (avoid waste)
The statistical study is built on the strategy of prevention. Based on the statistical study, there can be 3 key types of variation in the process
- Location (mean/central value)
- Spread (width/span)
- Shape (Pattern of variation-skewed, asymmetrical etc.)
The key goal is to maintain the location to the target value with minimal variability. There are 2 key types of causes for the variation in the process
- Common Cause: Variations that are consistently acting on the process. Produce a stable and repeatable distribution over time (in a state of statistical control)
- Special Cause (Assignable causes): Variations that affect only some part of the process output. Often intermittent and unpredictable.
Pre-condition for Cp and Cpk study:
- The process is stable and in statistical control
- Cp and Cpk should always be analysed together
- Cp values if significantly more than Cpk indicate an opportunity for improvement in centring the process
Following are some of the key difference between Cp and Cpk:
S.No. | Cp | Cpk |
1 | Cp is about Capability | Cpk is about Performance |
2 | This measurement is determined by dividing the specification limit (voice of the customer) by the process spread (voice of the process) | Compare the average of the data to both the upper and lower specification limit. |
3 | Indices of Process Variation only | Indices of Process Variation and Centering combined |
4 | Not impacted by the process location | Cpk will always be less than or equal to Cp |
5 | Calculated for only 2 sided (bilateral) tolerances | Cpk is calculated as the minimum of CPU and CPL |
6 | Indicates whether the process is capable of producing products to specifications | Determine whether the process is capable of meeting customer requirement or not |
7 | Cpk will be equal to Cp only when the process is centred |
Present Challenges:
- How often the user of statistical techniques is aware of the difference between Cp and CpK?
- How often the objective of the statistical study is understanding the variation in the process rather than achieving Cp and CpK values?
- Generally, statistical studies are conducted once a month or quarter but does it serve the process to monitor the variation in the manufacturing process or only to fulfil the requirement?
References:
IATF 16949: 2016
SPC Manual (AIAG) 2nd Edition
Industry Experts
This is the 106th article of this Quality Management series. Every weekend, you will find useful information that will make your Management System journey Productive. Please share it with your colleagues too.
Your genuine feedback and response are extremely valuable. Please suggest topics for the coming weeks.
Confusing terms, explained nicely with clarity.
Thanks Anju
Technique of explaining is superb.
Sir ,
Can you please us certified training on those topics.
Thanks Pradeep. DNV is conducting certified courses on the core tools.
Hello sir, learnt lot things from your videos. Happy to share feeling.
Pls make Another One video on MSA thoroughly.
Dear Momin, Thanks for your feedback and appreciation. There are few videos which can help you.
http://bit.ly/RepeatabilityReproducibility
https://youtu.be/QQWaxuHsLyE
https://youtu.be/ba_kvPRA6PA
http://bit.ly/BiasLinearity
https://youtu.be/KezLQ6IK0wo
https://youtu.be/WVa_CAzWeXY
good
Thanks Gopal
Good explanation of spc
Thanks Sonu for going through the video and liking it.