TPM (Total Productive Maintenance)
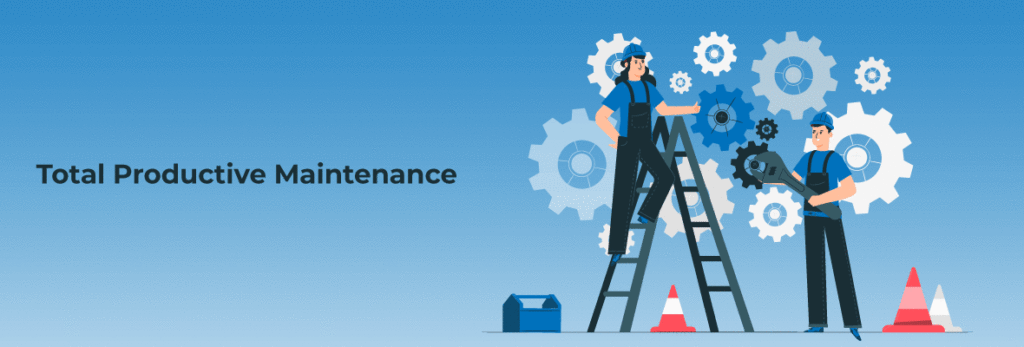
TPM (Total Productive Maintenance)
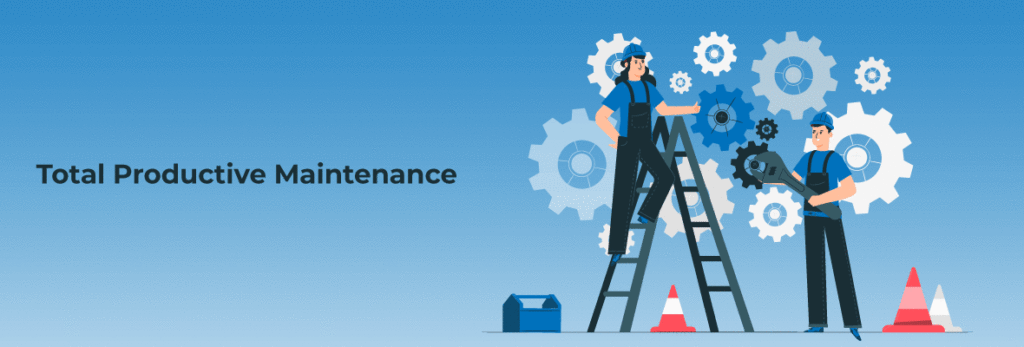
“TPM is the making of products through the making of people“: Seiichi Nakajima
Brief History of TPM
Seiichi Nakajima, regarded as the Father of TPM, describes the philosophy of TPM in a quote: “TPM is the making of products through the making of people”. The term OEE was invented in the 1960s (OEE=Availability x Productivity x Quality).
The goal of TPM: “Enhance the volume of the production, employee morale and job satisfaction.”
The Japan Institute of Plant Maintenance (JIPM) proposed the method for evaluation of organization for its effective implementation of TPM in 1971. It was initially incorporated and established at Nippon Electrical Equipment Co., Ltd (currently Denso Corporation).
What is TPM
TPM (Total Productive Maintenance) = Overall maintenance for manufacturing
It focuses on equipment and people and is a maintenance technique which improves productivity to achieve zero losses and reinforces production foundations.
Total: All departments, facilities and processes, the participation of all employees, aim to eliminate all accidents, defects, breakdown etc.
Productive: Maximization of efficiency of the production process, production as per customer expectations, minimize obstacles within the production process
Maintenance: Improvement in the efficiency of facilities and plant, continuous sustainment and improvement of plant and machinery, concerns the whole life cycle of the production system
3 Key objectives of TPM
Zero Breakdown
Zero Defect
Zero Accident
To achieve Just in Time (JIT) and Total Quality Management (TQM), effective implementation of TPM is must for the organization.
1) 5S – Sort, Straighten, Shine, Standardize and Sustain
Just like a physical structure starts with a grounded framework, building a strong TPM process requires a strong foundation in the form of the principles of 5S. This is a workplace organization method that is simplified into 5 basic steps:
- Sort tools, equipment, and materials to identify which of these can be discarded
- Straighten and set things in the proper order to reduce unnecessary motion and efficiently travel between working groups and locations
- Shine refers to performing necessary housekeeping to clean up the work area
- Standardize and schedule activities to systematically form the habits to keep the workplace organized
- Sustain the process and principles for long-term applications
The 5S approach provides a systematic approach to cleaning the workplace, thereby uncovering underlying problems and challenges.
2) Autonomous Maintenance (Jishu Hozen)
Maintenance tasks and caring for equipment should start with the people using the equipment. The empowerment of operators to work on small maintenance tasks effectively allows the maintenance teams to focus on more specialized assignments.
The Six Big Losses:
Availability: Unplanned Stops, Planned Stops
Productivity: Small Stops, Slow Cycle time
Quality: Production Rejects and Startup Rejects
3) Continuous improvement (Kobestu Kaizen)
Also known as the Japanese term Kaizen, it promotes the attitude of progressing towards zero losses and zero defects. Through small but continual tweaks to processes, the overall effectiveness and efficiency of the organization are developed.
4) Planned maintenance
Planned maintenance activities are essential to the prevention of equipment breakdown. Planned maintenance is performed by periodically evaluating the (condition-based and Time-Based) equipment to proactively prevent deterioration and mechanical failures.
5) Quality maintenance
To ensure the satisfaction of the customer, manufacturing processes aim for zero-defect production. Standards for superior quality and checks on whether the standards are being met, should be in place. The goal of quality maintenance is to identify any possible causes of deviations from zero-defect production. The Transition is from reactive to proactive (Quality Control to Quality Assurance).
6) Training
The idea of TPM is that everyone does their part to contribute to the overall productivity of the production process. In order to achieve optimum performance, and to build each member’s competence, proper training is required to equip each one with the theoretical and practical know-how of working with machines and equipment. It is not sufficient to know only “Know-How” but they should also learn “Know-why“.
7) Office TPM
A key role that is often overlooked is the administrative department that works behind the scenes. Like the rest of the production teams and processes, the management and administrative functions are also subject to productivity improvement. This includes identifying and eliminating losses and contributing to the overall performance of the plant.
8) Safety, health and environment
The last of the eight pillars focus on creating a safe workplace. The essence of this pillar is realized when actively applied to each of the other pillars. The successful implementation of this pillar will contribute to a secure and hazard-free workplace. The key objective is:
- Zero accident
- Zero health damage
- Zero fires
Why TPM is needed?
- To achieve productivity
- To achieve quality
- To achieve zero breakdown
Key factors for the Success of TPM
- Involvement and commitment of TOP MANAGEMENT
- TEI (Total Employee involvement)
Possible Benefits (PQCDSM)
- Productivity – It is improved through fewer losses in the company
- Quality – It is improved as a result, failures and malfunctions are reduced
- Cost: As overall equipment efficiency (OEE) increases, production costs are also minimized. Higher productivity leads to higher profits and reduced spending on equipment stoppage time and repairs
- Delivery – TPM leads to high delivery performance and customer satisfaction
- Safety – “Zero failure”, “zero defect” and “zero accident” conditions build employee self-confidence
- Employee Ownership – Ownership of equipment by operators through Autonomous Maintenance
- Improved working environment – Clean working conditions provide a good working environment Increased Plant Reliability
Challenges
- Lack of involvement of top management once the first level of TPM is implemented
- Attitude: I Operate; YOU Maintain!
- Manipulation of data to achieve TPM award!
- Lack of linkage of tangible benefits from TPM to the bottom line (profit) of the organization
References:
IATF 16949: 2016
This is the 72nd article of this Quality Management series. Every weekend, you will find useful information that will make your Management System journey Productive. Please share it with your colleagues too.
Your genuine feedback and response are extremely valuable. Please suggest topics for the coming weeks.
Well explained and very useful. Thanks a lot Mangla Sahab
Thanks Vinai
Thank you sir for sharing this information.
But I always confused in TPM system and Lean manufacturing system how it is different from each other ? any company will be follow both systems or just once? please explain in your new video.
Dear Atin, Thanks for your query and response. This question is not only true for this but for other methodologies like TQM/TPM. As per my understanding, Lean is more of a customer-focused, market-driven approach to Continuous Improvement and sometimes it is considered that TPM is a sub-set of Lean as TPM is a later step in the Lean journey.