New Product Development: Product & Process Validation (APQP-Phase 4) (Part 5 of 8)
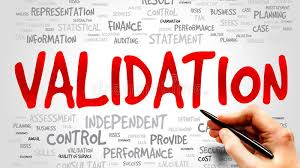
New Product Development: Product & Process Validation (APQP-Phase 4)
(Part 5 of 8)
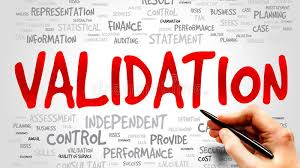
“Design is not just what it looks like and feels like. Design is how it works.” –Steve Jobs
Introduction
When we are in the process of buying a car, we test drive the vehicle to assess whether it will fulfil our expectations or not. Before marriage, both boy and girl try to spend some quality time together (also live-in) to assess the compatibility with each other. When we buy any dress, we generally do a trial fitting at the shop (although missing during online purchase).
Something similar happens in the validation phase, wherein organization validate their product before mass production.
Objective
Once the product and process design activities are completed, the next step is to validate the product whether the output of these activities are capable of meeting the customer requirements when the product is manufactured. Once the organization is satisfied with the output, the pilot product can be shipped to the customer for their further testing and approval. During this stage, gaps can also be identified when trial production is done using a process flow chart and control plan. These gaps should also be corrected before going for mass production.
Definitions
As per IATF 16949, clause 3.0, following are some of the key definitions related to the design process
Advanced product quality planning (APQP): product quality planning process that supports the development of a product or service that will satisfy customer requirements; APQP serves as a guide in the development process and also a standard way to share results between organizations and their customers; APQP covers design robustness, design testing and specification compliance, production process design, quality inspection standards, process capability, production capacity, product packaging, product testing and operator training plan, among other items.
Special characteristic: classification of a product characteristic or manufacturing process parameter that can affect safety or compliance with regulations, fit, function, performance, requirements or subsequent processing of the product.
Customer Specific Requirements (CSR) of IATF subscribing OEM
Following are their key requirements
Daimler:
Special Characteristics: MBST 13/18, section 5, paragraph 3 + 7
PPAP: MBST 13/18 complete Production Process and Product Approval (PPA)
Design and development changes – supplemental: MBST 13/18, section 4 MBST 13/18, section 5
FCA:
Design & Development: SQ.00010 Advance Quality Planning (AQP) and PPAP
Embedded Software: assessment of software process capability/maturity: as per CS.00187
GM:
PPAP: GM 1927-03 Quality SOR
Detailed Information
As per IATF 16949, Clause 8.3 and APQP manual (Advance Product Quality Planning- 2nd edition, July 2008), there are 5 key phases. They are
- Plan and define the program
- Product design and development verification
- Process design and development verification
- Product and process validation
- Feedback, assessment and corrective action
As per APQP manual, 2nd edition, following are some of the key inputs (which are output from Process Design phase)
- Specification and Drawing
- Process flow chart
- Floor plan layout
- Characteristics matrix
- Identification of error proofing
- Process Failure Mode and Effect Analysis (PFMEA
- Pre-launch Control Plan
- Process approval acceptance criteria
- Work Instructions
- Packaging standards
- Tooling and Equipment for the production Maintenance plan
- Measurement System Analysis plan (MSA)
- Preliminary Process Capability Study plan
- Data for quality, reliability, maintainability and measurability
- Methods of rapid detection, feedback, and correction of nonconformities
- Capacity analysis
- Product and process quality system review
- Management Support
Based on the above inputs, the following are the possible outputs from this phase which are further bifurcated into 3 parts, which are
Documentation Preparation
Process Validation
Product Validation
Documentation Preparation:
- Production Control Plan: It is a document which specifies the controls that need to be applied to the production parts and processes. It is a live document which is an outcome of the product and process design process. The production control plan is the output of the prelaunch control plan. The production control plan is generally approved by the customer initially and after any changes due to 4M (Man, Machine, Material, Method).
Apart from the AIAG manual, many customers have their template for the control plan.
- Competent manpower: For product and process validation process; identification, training and regular up-dation of competency of the concerned person will be very important for the successful effectiveness of this phase. All the relevant person should be trained for special skills like MSA, SPC, Special Characteristics, 4M change, fool proofing etc. Example: Competency for personnel working in Production, Quality, Testing, Logistics, Inspection etc.
Process Validation:
- Equipment and Tooling Trial: In this phase, the purchased equipment and tooling are put under trial to verify whether they are working as per their specification and can meet customer expectations.
- Significant production run: During this stage, the intent is to run the complete production process by using the same
- Process flow chart
- Control plan
- Production process
- Production tooling
- Production operators
- Production gauges and fixtures
- Production rate
So that it can be assessed whether an organization is ready for mass production? Many customers have their guidelines for the production trial run especially IATF (International Automotive Task Force) subscribing OEM (Original Equipment Manufacturer) but apart from them, majority of the OEM and tier 1 also have their supplier manual wherein they specify trial run quantity, quality level, operator competence and many more significant points. The organization can also define its specifications, if not provided by the customer. For effective validation, the timeline of the validation process should be aligned with customer timeline. Some of the key output of the production trial run includes
- Measurement system analysis results
- Process capability study
- Production rate (Run-a-Rate Study)
- Process review
- Product validation
- First-time capability
- Packaging evaluation
- Creation of limit samples and master samples
- Part Approval (PPAP-Production Part Approval Process)
- Measurement system evaluation (MSA): As per AIAG (Automotive Industry Action Group) manual or customer-specific requirement, MSA study for all the measuring instruments, gauges, test equipment etc. which are referenced in the control plan can be conducted. The intent is to verify the contribution of error due to measurement system. The MSA study includes measurement of repeatability, reproducibility, ndc (number of distinct characteristics) linearity etc.
- Preliminary process capability study: As per AIAG manual or customer-specific requirement, as per the plan, capability study for all the special characteristics (Critical, Major) which may impact the process and product characteristics can be carried out. The study intends to verify that during initial production trial run, whether the process is capable of meeting the product requirements and ready for the mass production.
Product Validation:
- Production validation testing: The key output of this phase is to get the assurance that the product is meeting all the customer and organization requirement. These outputs are related to meeting the engineering test when product is manufactured by using the processes and tooling which will finally be used in mass production too. As per the sampling plan, the validation of the product is conducted. Example: Vibration test, durability test, functional test, temperature test, Type test etc.
- Packaging evaluation: While dispatching the pilot lot to the customer, the packaging standard should fulfil all the requirements related to the protection of the product until it reaches the customer as well as environmental protection too. Effectiveness of packaging evaluation also includes meeting the customer requirements. Example: for packaging PCB (printed circuit board), both safety of the product from damage and protection from environmental factors like humidity and moisture is pertinent.
- Review of the legal requirements (statutory & Regulatory): Wherever customer or governmental agencies have specified any legal requirement for the product like Emission norms, it needs to be validated at this stage. These requirements are equally responsible for supplier & their sub-supplier too (entire supply chain). Example: Legal requirement of the country which shipped the component, the country which received the component and the final destination country which will use the final product.
- Embedded software: The percentage of embedded software in the automobile is significantly increasing. The same is true for other industries and their products too. At this stage, a systematic review of the effectiveness of the embedded software helps the organization to understand its performance during mass production too. The key thing is to validate the compatibility of embedded software with the final product at the customer end.
- Production part approval: As per AIAG manual 4th edition or customer-specific requirement, during production part approval process (PPAP), the intent is to understand and verify that whether all the customer requirements (design and process) have been understood and implemented by the organization. Moreover, whether the manufacturing process has the potential to produce the products consistently as per requirement while meeting the actual production run. During this stage, PPAP requirements from the supplier (Raw material and Bought-out components) is also verified for its effectiveness. The effectiveness of the processes and documentation from the supplier can also be done at supplier premises.
- Quality planning sign-off and management support: The key intent of final sign off is that the CFT (cross-functional team) will review and analyse that whether the product and process design inputs are incorporated in the final product or not. So, the organization is confident that they can manufacture, test, package and despatch the desired quality product to the customer on time. During this final phase, some of the key review by CFT includes
- Process Flow Chart (PFC): Effectiveness of PFC and its implementation
- Control plan: Whether it is appropriate to the product and meeting the intent
- Work instructions: Whether all the key requirements related to product, process and special characteristics are addressed effectively and can be utilized at the shop floor.
- Monitoring and measuring devices: As specified in the control plan, whether required gauges, fixtures and measuring instruments are available and meeting the calibration and MSA requirements.
- Required capacity achievement: As per the initial plan, whether the desired quantity can be produced to fulfil customer schedule.
- Required quality: As per the agreement, whether the desired quality level can be achieved to fulfil customer requirement.
- Required timeframe: As per agreed timing-plan, whether timeline as per customer requirement has been achieved.
Finally, the involvement of top management at regular internal as well as at completion is important. Wherever there are gaps, it can be escalated to the top management for their review.
Benefits to Organization:
- It will result in a smooth transition to mass production
- The possibility of failure at customer and user end will be limited
- The customer target related to product reliability and durability will be met
- It will be easier and quicker for the customer to do assembly and further testing at their end
- Customer satisfaction will be enhanced
Present Challenges:
- Sometimes initial line setup and approval is conducted by the team who are not part of the mass production team!
- The work environment wherein validation is conducted is quite different from a real-life situation
- The organization is not always competent and have an inadequate infrastructure to conduct a validation study.
- Generally, the sampling plan and inspection frequency for prelaunch and production control plan remain the same!
References:
ISO 9000: 2015
ISO 9001: 2015
IATF 16949: 2016
APQP 2nd Edition
This is the 78th article of this Quality Management series. Every weekend, you will find useful information that will make your Management System journey Productive. Please share it with your colleagues too.
Your genuine feedback and response are extremely valuable. Please suggest topics for the coming weeks.
Recent Comments