New Product Development: Feedback, Assessment & Corrective Action (APQP-Phase 5)
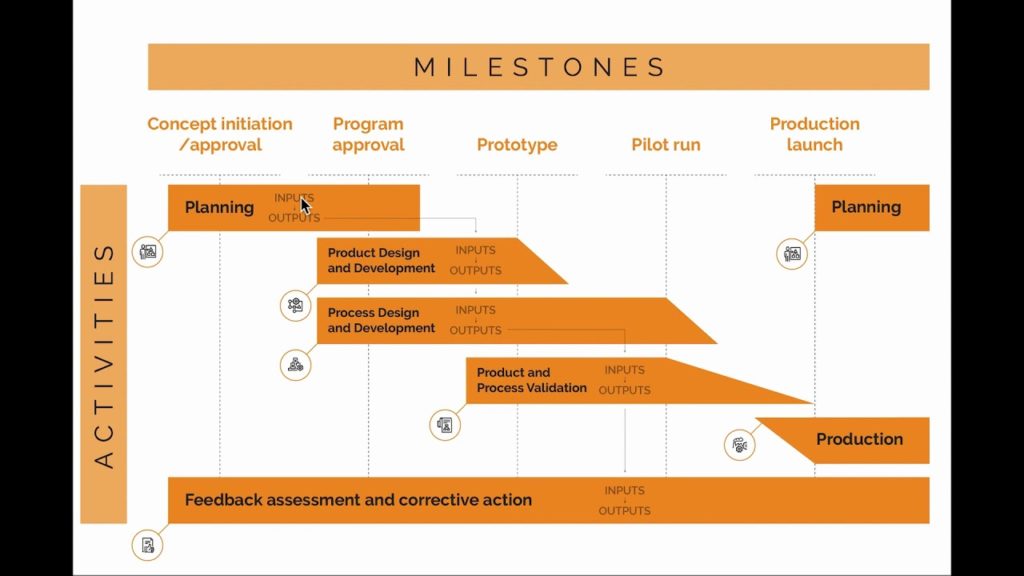
New Product Development: Feedback, Assessment & Corrective Action
(APQP-Phase 5)
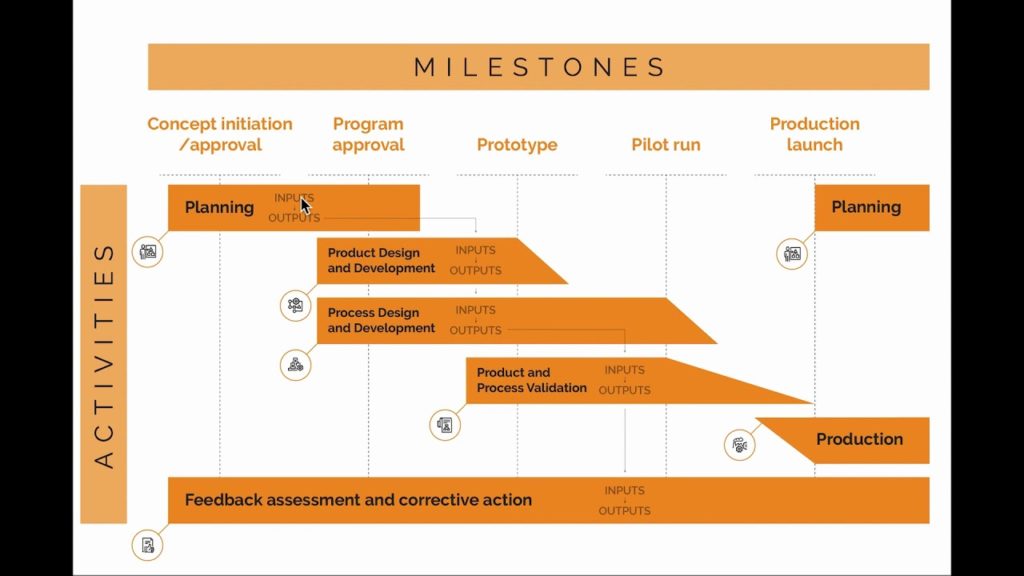
“Feedback is the breakfast of champions.” – Ken Blanchard
Introduction
As human beings, we are generally good in implementing certain things but either we are averse for the feedback or we do not feel any more improvement is possible. As per PDCA (Plan, Do, Check, Action) cycle, unless ‘Checking’ and ‘Action’ is taken, the effectiveness of the ‘Plan’ and ‘Do’ will never be sustainable.
Objective
This phase intends to analyse the effectiveness of the first 4 phases and how it has translated the requirements into a good quality product/service which can meet the organization’s and customer’s requirement. Wherever gaps are observed, they need to be analysed and acted upon so that customer satisfaction can be ensured.
Feedback, assessment and corrective action is a common thread from the planning stage till final handover of the product for mass production. When a customer shares their requirement to the organization, the process of feedback and assessment initiates. Based on customer response, wherever needed, corrective actions are taken at different stages.
Definitions
As per IATF 16949, clause 3.0, following are some of the key definitions related to the design process
Advanced product quality planning (APQP): product quality planning process that supports the development of a product or service that will satisfy customer requirements; APQP serves as a guide in the development process and also a standard way to share results between organizations and their customers; APQP covers design robustness, design testing and specification compliance, production process design, quality inspection standards, process capability, production capacity, product packaging, product testing and operator training plan, among other items.
Special characteristic: classification of a product characteristic or manufacturing process parameter that can affect safety or compliance with regulations, fit, function, performance, requirements or subsequent processing of the product.
Customer Specific Requirements (CSR) of IATF subscribing OEM
Following are their key requirements
Daimler:
Special Characteristics: MBST 13/18, section 5, paragraph 3 + 7
PPAP: MBST 13/18 complete Production Process and Product Approval (PPA)
Design and development changes – supplemental: MBST 13/18, section 4 MBST 13/18, section 5
FCA:
Design & Development: SQ.00010 Advance Quality Planning (AQP) and PPAP
Embedded Software: assessment of software process capability/maturity: as per CS.00187
GM:
PPAP: GM 1927-03 Quality SOR
Detailed Information
As per IATF 16949, Clause 8.3 and APQP manual (Advance Product Quality Planning- 2nd edition, July 2008), there are 5 key phases. They are
- Plan and define the program
- Product design and development verification
- Process design and development verification
- Product and process validation
- Feedback, assessment and corrective action
As per APQP manual, 2nd edition, following are some of the key inputs (which are output from Product & Process Validation phase)
- Production Control Plan
- Competent manpower
- Equipment and Tooling Trial
- Significant production run
- Measurement system evaluation (MSA)
- Preliminary process capability study
- Production validation testing
- Packaging evaluation
- Review of the legal requirements (statutory & Regulatory)
- Embedded software
- Production part approval
- Quality planning sign-off and management support
Based on the above inputs, the following are the possible outputs from this phase, which are
- Reduced variation: While assessing the performance of pilot lot and mass production with the customer, understanding the variation in the product performance is key. It may be due to common and special causes. By using SPC techniques like control chart, an organization can understand the variations and take actions. The actions should also include improvement in cost reduction, the timing for the development and any other feedback received from the customer. For continual improvement activities like cost reduction, tools like VA (Value analysis) and VE (Value Engineering) can be used.
- Improved customer satisfaction: Based on the feedback of pilot lot production, the organization may get a response from the customer for changes in the process or defects in the product. During this stage, both organization and customer can work together to improve the product quality and manufacturing processes. It will finally help to improve customer satisfaction.
From phase 1 onwards, where the voice of the customer is shared with the organization, systematic and timely response from the organization can ensure that customer remains satisfied with the intent of the organization.
- Improved delivery and services: The intent is not only to improve the quality and delivery of the products which are directly going to the customer but also the spare parts and after-sales service too. Although the goal is ‘First Time Quality-FTQ’ but there is always a possibility of getting customer complaint from the factory or end-user. In such cases, both organization and customer can work together to analyse the problem and take realistic actions.
From phase 1 onwards, where customer requirements and customer-specific requirements are shared with the organization, timely response about the queries and issues related to product and process design forms the foundation of effective delivery performance from organization.
- Effective use of lesson learnt / Best practices: During the development process, there is always some possibility of failures like not meeting timing plan, poor quality performance, high cost etc. The organization can have a formal system of capturing all the learning from the development process so that they can be avoided in the next development. Some of the key inputs related to the lesson learnt includes
- Warranty data
- Recall
- Delivery failures
- The high cost of production
- Low FTQ
- Customer complaints
- Proposed corrective actions
Learning from past experiences should be an ongoing process. Apart from learning from previous development, the experience shared during the development cycle can also be a good input for the lesson learnt.
Benefits to Organization:
- Enhanced customer satisfaction
- Improvement in FTQ (First Time Quality)
- Improvement in the understanding of the cross-functional team (CFT)
- Better value creation for the customer
- Reduced iteration of development at organization end
Present Challenges:
- How often systematic capturing of the lesson learnt is done by CFT?
- How often the identified lesson learnt is understood and implemented in the upcoming projects?
- How often top management is involved in understanding the performance of QCD (Quality, Cost and Delivery) from the original target?
References:
ISO 9000: 2015
ISO 9001: 2015
IATF 16949: 2016
APQP 2nd Edition
This is the 79th article of this Quality Management series. Every weekend, you will find useful information that will make your Management System journey Productive. Please share it with your colleagues too.
Your genuine feedback and response are extremely valuable. Please suggest topics for the coming weeks.
Recent Comments