New Product Development Process
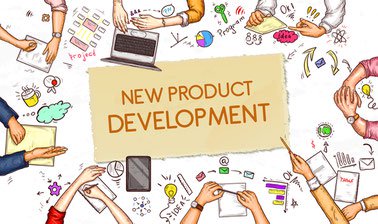
New Product Development Process
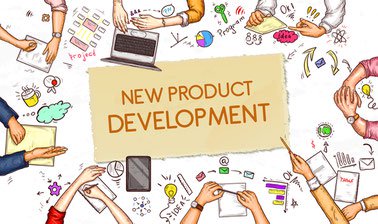
“You have got to start with the customer experience and work back towards the technology- not the other way around”: Steve Jobs
Introduction
‘Necessity is the mother of invention.’ For mathematical calculation, zero (0) was invented and used by Aryabhata (499 BC). The curiosity of man to fly like birds resulted in the invention of Aeroplan. In the last 50 years, some of the popular inventions include the computer, the Internet & the mobile phone. Chefs are popular for creating new dishes from the same vegetables as potatoes.
In the automobile sector, new vehicles are designed to cater to/create a new market. A systematic approach for the design and development of any product or its component ensure that product is reliable and meets the expectation of the user.
Objective
In this blog, you will understand (as per APQP manual), what are 5 different phases of the new product development process, key inputs and output of each phase, possible benefits and present challenges.
Definitions
As per IATF 16949, clause 3.0, following are some of the key definitions related to the Design process
Advanced product quality planning (APQP): product quality planning process that supports the development of a product or service that will satisfy customer requirements; APQP serves as a guide in the development process and also a standard way to share results between organizations and their customers; APQP covers design robustness, design testing and specification compliance, production process design, quality inspection standards, process capability, production capacity, product packaging, product testing and operator training plan, among other items.
Customer requirements: all requirements specified by the customer (e.g., technical, commercial, product and manufacturing process-related requirements, general terms and conditions, customer-specific requirements, etc.)
Customer-Specific requirements (CSRs): interpretations of or supplemental requirements linked to a specific clause(s) of this Automotive QMS Standard.
Design-responsible organization: the organization with authority to establish a new, or change an existing, product specification. This responsibility includes testing and verification of design performance within the customer’s specified application.
Design Verification-DV (Clause: 8.3.4.2- FCA) is a series of tests, inspections, and procedures that must be accomplished to determine if the design meets its intent.
Production Validation-PV (Clause: 8.3.4.2-FCA) is a series of tests validating the production tooling, methods, and processes used to manufacture a component.
Customer Specific Requirements (CSR)
For IATF subscribing OEM’s following are their requirements
Daimler:
Special Characteristics: MBST 13/18, section 5, paragraph 3 + 7
PPAP: MBST 13/18 complete Production Process and Product Approval (PPA)
Design and development changes – supplemental: MBST 13/18, section 4 MBST 13/18, section 5
FCA:
Design & Development: SQ.00010 Advance Quality Planning (AQP) and PPAP
Embedded Software: assessment of software process capability/maturity: as per CS.00187
GM:
PPAP: GM 1927-03 Quality SOR
Detailed Information
As per IATF 16949, Clause 8.3 and APQP manual (Advance Product Quality Planning- 2nd edition, July 2008), there are 5 key phases. They are
- Plan and define the program
- Product design and development verification
- Process design and development verification
- Product and process validation
- Feedback, assessment and corrective action
Some of the key input and output for each phase is as follows
- Plan and Define Program: In design and development planning process, the key intent is to understand the end objective in terms of Quality, Cost and Time (QCD) & design the entire development process accordingly. Once the organization has effectively planned the design and development stages, the possibility of achieving the desired target augments.
Key Inputs:
- Voice of the customer (Market research, historical warranty data, past experience)
- Marketing strategy
- Product and process benchmark and assumptions
- Product reliability studies
- Embedded Software Requirement
- Applicable statutory and regulatory requirements
- Targets for conformity to product requirements including preservation, reliability, durability, serviceability, health, safety, environmental, development timing and cost
- Identification, traceability and packaging
- Product specifications
- Previous design projects, competitor product analysis (benchmarking), supplier feedback, internal input, field data and other relevant sources for current and future projects of a similar nature
Key outputs:
- Design Goals
- Reliability and Quality Goals
- Preliminary Bill of Material
- Preliminary Process Flow Chart
- Preliminary identification of special characteristics: products and processes
- Product Assurance Plan
- Management Support
- Product Design and Development Verification: In the product design process, the key intent is to understand all the input requirements like the voice of the customer (volume, historical warranty, previous experiences, design goals) and convert them into feasible product design. It should be able to meet the customer volume, quality, investment cost, timing target and other relevant requirements.
Key Inputs: The output of phase 1 becomes key inputs for phase 2
Key Outputs:
- Engineering drawing & specifications
- Material Specifications
- Design Failure Modes & Effect Analysis (DFMEA)
- Special product and process characteristics
- Design for Manufacturability and Assembly (DFM, DFA)
- Design Verification
- Design Review
- Prototype Control Plan
- Drawing and specification change
- New equipment, tooling and facilities requirement
- Gauges / Test Equipment requirements
- Reliability study
- Service diagnostic guidelines and repair and serviceability instructions
- Service part requirements
- Team Feasibility commitment and Management support
- Process Design and Development Verification: In this phase, based on the product related inputs from phase 2 and customer, the process is designed so that product can be manufactured which can meet customer requirements.
Key Inputs: The output of phase 2 becomes key inputs for phase 3
Key Outputs:
- Product and process quality system review
- Process flow chart
- Specification and Drawing
- Floor plan layout
- Capacity analysis
- Characteristics matrix
- Process Failure Mode and Effect Analysis (PFMEA)
- Pre-launch Control Plan
- Work Instructions
- Measurement System Analysis plan (MSA)
- Process approval acceptance criteria
- Preliminary Process Capability Study plan
- Packaging standards
- Tooling and Equipment for production
- Maintenance plan
- Data for quality, reliability, maintainability and measurability
- Identification of error proofing
- Methods of rapid detection, feedback, and correction of product/manufacturing process nonconformities
- Management Support
- Product and Process Validation: Once the product and process design activities are completed, the next step is to validate the product whether these activities are capable of meeting the customer requirements when the product is manufactured. Once the organization is satisfied with the output, the pilot product can be shipped to the customer for their testing and approval. During this stage, gaps can also be identified when trial production is done using a process flow chart and control plan. These gaps should also be corrected before going for mass production.
Key Inputs: The output of phase 3 becomes key inputs for phase 4
Key Outputs:
- Significant production run
- Measurement system evaluation (MSA)
- Preliminary process capability study
- Production part approval (PPAP)
- Production validation testing
- Packaging evaluation
- Production Control Plan
- Review of the legal requirements (statutory & Regulatory requirements)
- Embedded software
- Quality planning sign-off and management support
- Feedback, Assessment and Corrective Action: This phase intends to analyse the effectiveness of the first 4 phases and how it has translated the requirements into a good quality product/service which can meet the organization’s and customer’s requirement. Wherever gaps are observed, they need to be analysed and acted upon so that customer satisfaction can be ensured.
Feedback, assessment and corrective action is a common thread from the planning stage till final handover of the product for mass production. When a customer shares their requirement to the organization, the process of feedback and assessment initiates. Based on customer response, wherever needed, corrective actions are taken at different stages.
Key Inputs: The output of phase 4 becomes key inputs for phase 5
Key Outputs:
- Reduced variation
- Improved customer satisfaction
- Improved delivery and services
- Effective use of lesson learnt / Best practices
Possible Benefits:
- Target for Quality, Cost and Time will be achieved
- Customer and relevant stakeholders will be satisfied
- Employee morale will enhance
- Relationship and trust with the customer will improve
Present Challenges:
- How often the cross-functional team (CFT) is competent to understand 5 phases of APQP?
- How often CFT is defined and work is done as a team during development?
- How often timing plan is reviewed and updated periodically and after any change?
- How often systematic reviews are conducted at a periodic interval and after each phase?
- How often regular and updated feedback is shared with top management as management review input?
References:
ISO 9000: 2015
ISO 9001: 2015
IATF 16949: 2016
APQP 2nd Edition
This is the 74th article of this Quality Management series. Every weekend, you will find useful information that will make your Management System journey Productive. Please share it with your colleagues too.
Your genuine feedback and response are extremely valuable. Please suggest topics for the coming weeks.
Nicely explained. quality function deployment or the house of quality would also play a major role in new product development.
Very true Gaurav. There are many good techniques like QFD. Thanks for the response.
Great to learn from you mangla sir…… expecting some more learning in future ??
Sure Prasad. Do continue to share your feedback