Managing Your Workload: A Guide to Daily Work Management (DWM)
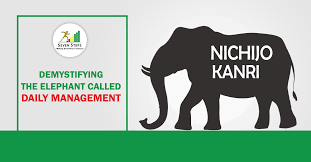
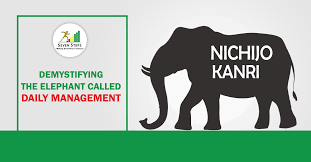
“A tree starts with a seed”: Indian Proverb
Introduction
Someone has rightly said, ‘an apple a day keeps the doctor away.’ For a healthy heart and body, the doctors recommend a 40-minute brisk walk every day. My father told me the same thing. ‘Once a task is just begun, never leave it till it’s done. Be the labour great or small, do it well or not at all.’ You must have seen that a person who is regularly going to the gym can make a great body and lose weight but if the practice is not sustained, very soon, the health will deteriorate.
Read More: https://bit.ly/QualityCircle
Objective
Things do not stay there, they deteriorate. Can we have a status Quo without improvement? The answer is No. Therefore, small-small but continual improvement is required to maintain the good condition of processes, machines & equipment, etc. for business success.
Daily Work Management (DWM) is defined as the system that provides the ability to manage departments, functions, and processes, wherein processes are defined, standardized, controlled, and improved by the process owners. In an organization, it is very important to ensure that whatever procedure has been designed and implemented, it should be systematically followed.
Once you read this blog, you will understand the true meaning of Daily Work Management (DWM), how to implement it at your workplace successfully, the goal of DWM, why it is important and the possible benefits.
Read More: https://bit.ly/DOJOCentre
Definition:
Competence (ISO 9000: 2015, Cl 3.10.4): Ability to apply knowledge and skills to achieve intended results
Skill (ISO 30401: 2018, Cl 3.30): Learned capacity to perform a task to a specified expectation
Knowledge (ISO 30401: 2018, Cl 3.25): Human or organizational asset enabling effective decisions and actions in the context
Read More: https://bit.ly/5SSteps
Detailed Information
What is Daily Work Management (DWM)?
We are what we repeatedly do. Excellence then is not an act but a habit – Aristotle
In the present challenging times, no one can afford to rest on their past laurels, and we are all struggling for improvement. The western concept of improvement is to rely on innovation to achieve results – new products, new processes, and new equipment. Although it gives instant results, this tends to be unsettling, costs money and often doesn’t meet expectations.
The concept of daily work management is basically to regularly reach out to each & every person working at various levels so that a structured review mechanism where a formal discussion is facilitated related to details and communication.
Read More: https://bit.ly/KaizenMasaakiImai
Henry David Thoreau said, “It is not enough to be busy… The question is: what are we busy with?” An important aspect is that the DWM should be done on a day-to-day basis. This ensures that daily jobs and objectives are accomplished strictly on regular basis. There should be a perfect control system built into daily routine activity management which should not ordinarily allow any slip-up on daily plans, activities and results. Mike Rother, the author of Toyota Kata “Everything deteriorates over time; there is no stable condition that can be maintained. The only solution is to improve constantly”
Example: The organization may have implemented TPM (Total Productive Maintenance) in their organization and won the prestigious TPM Excellence award. Now, if the organization does not continue to work on their machine every single day (CLIT: Cleaning, Lubrication, Inspection, Tightening), the performance of the machine and related processes will start deteriorating.
There are two important roles of leaders in every organization. The first role is to run the day-to-day business smoothly and the second role is to work on strategic goals to achieve the organization’s vision. The first role is called Daily Management or Nichijo Kanri and the second role is called Policy Deployment or Hoshin Kanri. Both originated in Japan and adapted across the world.
Hoshin Kanri symbolizes the PDCA (Plan-Do-Check-Act) cycle in the KAIZEN perspective, while Nichijo Gemba Kanri represents the SDCA (Standardize-Do-Check-Act) cycle. Nichijo Gemba Kanri (SDCA) is, therefore, necessary for Hoshin Kanri (PDCA).
In other words, Daily Management is focusing on short-term and Policy deployment in the long term. They complement each other and we cannot ignore either of them. Lack of Daily Management causes firefighting and Lack of Policy deployment cause stagnant business growth.
Daily Work Management is a system that allows us to know on a daily basis whether we are on track or off track to meet our goals, take corrective action, and check that past actions and improvements are being sustained.
Read More: https://bit.ly/ROI-Training
What is the Purpose of DWM?
The expectations of the customer are everchanging. The priorities of the relevant interested parties like government bodies, society, financial institutions, pollution boards etc. are amending at a frequent pace. Under such circumstances, taking a new initiative is a big challenge and if the initiative is successful, making sure to keep it sustained is a much more daunting task. So, the intent of daily work management becomes even more important, wherein the focus is on maintaining compliance and improving it further on a day-to-day basis.
Read More: https://bit.ly/Kirkpatrick4LevelModel
The purpose of Daily work management (Nichijo Gemba Kanri: Japanese) is to make everyone come at a common platform, take charge and ownership of every aspect, for example, improving production, productivity, material availability, etc., and most importantly increasing communication. Any deviation in the daily routine activity management may mean a “dissatisfied customer.”
The common problems with the client and interested parties include:
- Recurring Problems (which are solved again and again)
- Inability to maintain Improvements
- Ineffective implementation of 5S (Seiri, Seiton Seiso, Seiketsu, Shitsuke)
- High Changeover time
- Operator mistake” or “Operator not trained”
- Unable to meet previously achieved targets
- Surprises
- Month End Pressures
Read More: https://bit.ly/TrainerCompetency
How to Effectively Implement DWM?
The Standardize – Do – Check – Act (SDCA) cycle is a follow-up cycle for sustenance ensuring that the improvements that have been achieved via Plan – Do – Check – Act (PDCA) cycle, do not slide back. SDCA and PDCA cycles are part of Deming’s improvement formulae where, PDCA leads to improvement and SDCA prevents deterioration, respectively. Hence, both the SDCA & PDCA cycles must be well established.
A process needs to be stabilized through standardization to make it more measurable, predictable, and controllable. Improvements cannot and must not be made to a process unless it is stable.
SDCA
- Standardization, the definition and documentation of operating procedures, process requirements, and other process specifications to ensure that the process is always executed in a standard and repeatable manner
- Doing, the defined standards
- Checking, the act of verifying if conformance to the standards results in process stability
- Action, which is the response appropriate for the observed effects of the standards.
In step 4 (Action), if the process has become stable with the implementation of the standards, then the standards are made permanent and even deployed more widely.
Read More: https://bit.ly/CompetencyMapping1
Who Should Participate in DWM?
EVERYONE
If a department/process is starting DWM activities, managers and all other employees should be included. If anyone is left out, this could lead to confusion or it will give the message to the employees that it is not their ownership. When people see their superiors taking DWM seriously by participating in it, they’ll be more likely to take it seriously, too.
Some people may play a bigger role in DWM than others, which is fine. There might be DWM coordinators who are in charge of installing and maintaining it, keeping track of assigned tasks, or introducing new department members to the DWM. Daily Work Management might initially take place as an event, but ideally, it becomes a part of daily work for everyone.
Read More: https://bit.ly/TraningNeedIdentification
Read More: https://bit.ly/CompetencyRequirement
Benefits of DWM
Provides data on where you are (actual) compared to where you want to go (planned)
- Assists with meeting customer demand
- Improves process quality
- Reduces process variation
- Ensures effective problem-solving
- Help standardize the way organizations manage their facilities
- Ensures sustainability for improvement efforts
- Prevents any surprises
Read More: https://bit.ly/EmployeeSatisfaction1
Industry Challenges:
- How often the systematic approach of Daily Work Management (DWM) is understood by the management or it is based on the random monitoring of the processes?
- How often a systematic review of the effectiveness of DWM is monitored by the management or the management does not feel the importance of monitoring the benefits by implementing the good practices of DWM?
Read More: https://bit.ly/DifferenceCoachingMentoring
References:
ISO 9001: 2015
ISO 9002: 2016
ISO 9004: 2018
IATF 16949: 2016
Industry Experts
This is the 175th article of this Quality Management series. Every weekend, you will find useful information that will make your Management System journey Productive. Please share it with your colleagues too.
In the words of Albert Einstein, “The important thing is never to stop questioning.” I invite you to ask anything about the above subject. Questions and answers are the lifeblood of learning, and we are all learning. I will answer all questions to the best of my ability and promise to keep personal information confidential.
Your genuine feedback and response are extremely valuable. Please suggest topics for the coming weeks.
Recent Comments