What is the key difference between the Different Attribute Control Chart (p, np, c, u)?
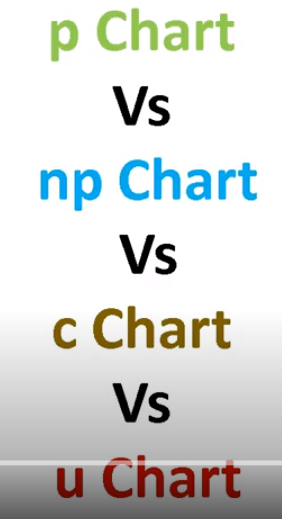
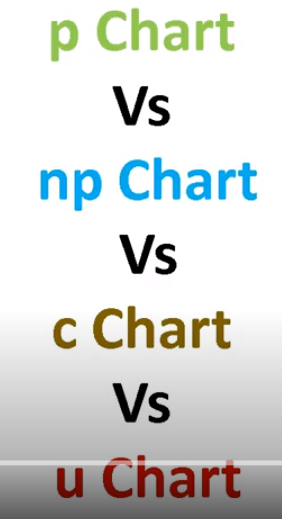
There’s a difference between being liked and being valued. A lot of people like you. Not many value you. Be Valued.: Unknown
Introduction
If the difference of opinion is always bad? It depends upon the situation. In some scenarios, it may result in conflict and delay the decision-making process. But, on the other side, it may bring out the best. So, it is not the differences that are bad but how we are handling them!
Objective
In the statistical studies, Walter Shewhart and W Edward Deming have done tremendous work to understand the variation in the process and its causes through statistical studies. The understanding of these variations is important to improve quality, increase productivity and reduce cost (QCD).
There are different types of attribute control charts that are plotted based on the type of data and criticality of the problem (p, np, c, u). By understanding these charts and taking suitable actions, the process can be brought under statistical control.
Definitions:
Attribute Chart: They have discrete values and can be counted for recording and analysis.
Detailed Information
Dr. Walter Shewhart developed the first control chart in the 1920s to describe common and special causes for Detection (tolerates waste) and Prevention (avoid waste).
Control charts can be used to monitor or evaluate the process. There are two types of control charts: Variable data and Attribute data.
The process itself will dictate which type of control chart needs to be used. While introducing the control chart, it is important to prioritize the problem area and use it where it is most needed. Example: If we want to measure the scratches or dents, they can not be measured. In such cases, these defective/defects can be counted and the attribute control chart can be plotted.
Before Attribute Control charts are used, several preparatory steps are needed like
- Establish an environment suitable for action
- Define the process
- Define the characteristic
- Define the measurement system
- Minimize unnecessary variation
- Define characteristics for the control chart like customer needs, current/potential problem areas, the correlation between characteristics
How to decide which Attribute control chart has to be used?
- p, np: Number of defective items
- c, u: Number of defects/unit
Following are some of the key difference between p, np, u, c Attribute Control Chart:
S.No. | p | np |
1 | Proportion of defectives | Process mean |
2 | Variable sample size | Constant sample size |
3 | The number of defectives in sample f, divided by the sample size n | Sum of the number of defectives, divided by the total number of sample N |
4 | Preferably do not vary by more than ± 25% of the average sample size | During Startup in the Moulding or Machining process |
5 | Binomial Distribution | |
6 |
Number of Defectives (Non-conforming) |
S.No. | u | c |
1 | Defects per sample unit | Process mean (Lot) |
2 | Variable sample size | Constant sample size |
3 | The number of defects in sample c, divided by the sample size n | Sum of the number of defects per sample unit, divided by the number of samples N |
4 | Preferably do not vary by more than ± 25% of the average sample size | During Startup in the Moulding or Machining process |
5 | Poisson Distribution | |
6 | Number of Defects |
Present Challenges:
- How often the organization is clear about the difference between p, np, c, u charts?
- Why the majority of the organization use only variable control charts and not attribute control charts?
References:
IATF 16949: 2016
SPC Manual (AIAG) 2nd Edition
Industry Experts
This is the 109th article of this Quality Management series. Every weekend, you will find useful information that will make your Management System journey Productive. Please share it with your colleagues too.
Your genuine feedback and response are extremely valuable. Please suggest topics for the coming weeks.
Recent Comments