Relationship of ISO/TS 9002: 2016 with ISO 9001: 2015
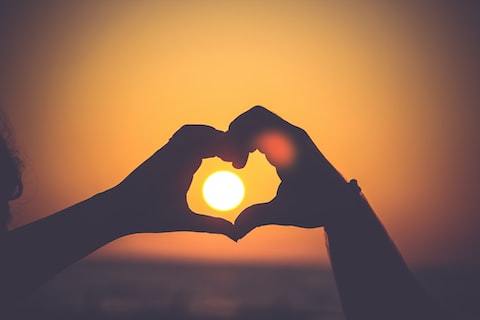
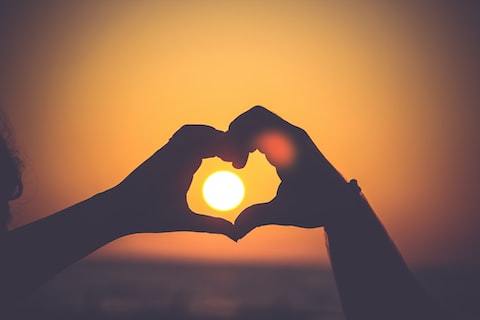
“A True relationship is two imperfect people refusing to give up on each other” ― Unknown.
Introduction
These days the relations have become very fragile. Till 2 decades back, the sustenance of relationships was high but of late, it has deteriorated very fast. There can be different reasons which can be attributed to it and it can lead to futile debate which may not give any reasonable solution. Even if we acknowledge this as a problem, we have started on the path of transformation.
Read More: https://bit.ly/ISO9001Series
Content: Attribute MSA Study
- What is ISO 9001?
- What is ISO/TS 9002: 2016?
- What is the Relationship between them?
- Conclusion
Objective
The ISO 9000 series provides a globally recognized framework for organizations to establish effective quality management systems. By implementing these standards, organizations can enhance their operational efficiency, meet customer requirements, and drive continual improvement.
Once you read this blog, you will understand, what is ISO 9001: 2015, what is ISO/TS 9002: 2016, what is its purpose of it and their interrelationship.
Read More: https://bit.ly/ISO9001Series
Definition: ISO 9000: 2015
Organization (Cl 3.2.1): Person or group of people that has its own functions with responsibilities and authorities and relationship to achieve its objectives.
Customer (Cl 3.2.4): Person or organization that could or does receive a product or a service that is intended for or required by this person or organization.
External Provider (Cl 3.2.6): Provider that is not part of the organization.
Quality Management (Cl 3.3.4): Management with regard to quality
Read More: http://bit.ly/CommonSpecialCause
Detailed Information
In the ISO 9000 series, the most popular standard is ISO 9001:2015 – Quality Management System – Requirements. There are 3 more standards which are closely related to ISO 9001:2015. They are:
- ISO 9000:2015 – Quality Management System: Fundamentals and Vocabulary
- ISO/TS 9002:2016 – Quality Management System: Guidelines for the application of ISO 9001:2015
- ISO 9004: 2018 – Quality Management – Quality of an organization – Guidance to achieve sustained success.
The above three standards directly and indirectly interact with the base standard ISO 9001: 2015. Only ISO 9001 is a certifiable standard. It means an organization can be certified by a third party (like DNV) only for ISO 9001:2015.
There are many other standards which are related to ISO 9001, including ISO 19011 (Internal Audit), ISO 31000 (Risk Management) and ISO 10000 series. All these standards have been developed by ISO/TC 176.
The linkage and relationship with ISO/TS 9002: 2016 are as follows
Read More: https://bit.ly/ISO9000Standard
What is ISO/TS 9002: 2016 (As per www.iso.org)
- ISO/TS 9002:2016 guides the intent of the requirements in ISO 9001:2015, with examples of possible steps an organization can take to meet the requirements. It does not add to, subtract from, or in any way modify those requirements.
- ISO/TS 9002:2016 does not prescribe mandatory approaches to implementation or provide any preferred method of interpretation.
- For the organization, consultants and certification body, it provides a rational basis to explain the interpretation of the ISO 9001 standard. It helps to understand the type of objective evidence that needs to be generated to fulfil a requirement. This Standard helps to reduce or remove any ambiguity about the understanding of the ISO 9001 standard within organizations, consultants and certification bodies.
Read More: http://bit.ly/TypeITypeIIError
Examples of ISO/TS 9002:2016 Interpretation
S.No. | Clause No. | ISO 9001 | ISO/TS 9002 GUIDELINES |
1 |
4.1: Understanding the organization and its context
|
The organization shall determine external and internal issues that are relevant to its purpose and strategic direction and that affect its ability to achieve the intended result(s) of its quality management system.
|
– either positively or negatively
– aware that external and internal issues can change – Sources of issues: Meetings, national & international press, websites, government departments, professional & technical publications, conferences, customers and relevant interested parties and professional associations – External issues could be Economic, social, political, technology, market and legal – Internal issues could be organization performance, resources, human aspect and governance |
2 | 4.2: Understanding the needs and expectations of interested parties | The organization shall determine:
a) the interested parties that are relevant to the quality management system. b) the requirements of these interested parties. The organization shall monitor and review information about these interested parties and their relevant requirements.
|
– beyond just those of its direct customers
– Consider its external and internal issues BEFORE – Interested parties: Customer, end-user, franchisor, shareholder, banker, union, supplier, employee, legal bodies, competitor, neighbour, local community – Method to know needs and expectations: Order received, legal compliance, benchmarking, market surveillance, supply chain relationship, customer survey and satisfaction – Relevant interested party’s requirements include Customer requirements, pricing, delivery, contracts, industry standards, MOU, protocol, code of practice, policies, environmental committees, Legal body |
3 | 6.1: Actions to address risks and opportunities | The organization shall consider the issues referred to in 4.1 and the requirements referred to in 4.2 and determine the risks and opportunities that need to be addressed.
The organization shall plan: a) actions to address these risks and opportunities. b) how to: 1) Integrate and implement the actions into its QMS processes 2) evaluate the effectiveness of these actions.
|
– purpose is to prevent nonconformities, including nonconforming outputs, and to determine opportunities that might enhance customer satisfaction or achieve an organization’s quality objectives.
– Example of Risk: QMS will not achieve its objectives including the failure of processes, products and services to meet their requirements, or the organization not achieving customer satisfaction. –Example of Opportunities: Potential to identify new customers, to determine the need for new products or services and to bring them to market, or to determine the need for revising or replacing a process by the introduction of new technology to become more efficient. – Techniques to determine Risk and opportunities: SWOT or PESTLE, Failure Mode and Effects Analysis (FMEA); Failure Mode, Effects and Criticality Analysis (FMECA); or Hazard Analysis and Critical Control Points (HACCP). Simpler approaches include brainstorming, Structured What If Technique (SWIFT) and consequences/probability matrices. – Action to address the Risk: Avoid it, eliminate it, take the risk, share the risk, no action |
4 | 7.4: Communication | The organization shall determine the internal and external communications relevant to the QMS, including:
a) on what it will communicate. b) when to communicate. c) with whom to communicate. d) how to communicate. e) who communicates. |
– Determine those relevant internal and external parties with whom they need to communicate
– Different communication methods are often required for different situations – formal communication such as reports, specifications, invoices or service level agreements for external relevant interested parties. – For internal communication, methods such as daily contact, regular department meetings, briefing sessions, email or an intranet. – To be effective, the organization’s communication processes should provide it and its persons with the ability to: – transmit and receive information quickly and act on it. – build trust amongst each other. – transmit the importance of customer satisfaction and process performance. – Identify opportunities for improvement. |
5 | 8.5.3: Property Belonging to the Customer or External Providers | shall identify, verify, protect and safeguard customers’ or external providers’ property.
When the property is lost, damaged or otherwise found to be unsuitable for use, report & retain documented information |
– Example: Equipment that is used for packaging or personal data
– Property can be tangible or intangible (material, tools, customer premises, intellectual property or personal data). – Examples: Instrument for measurement, vehicle for service or repair, component for PCB, packaging for finished goods, financial or personal data – Protection of customer property: Password protection, specific location to store intellectual property like drawing, software, Limited access, system for storage and deletion |
6 | 8.7.1: Control of Non-conforming Products | The organization shall ensure that outputs that do not conform to their requirements are identified and controlled to prevent their unintended use or delivery.
Take appropriate action based on the nature of the nonconformity in one or more of the following ways: a) correction. b) segregation, containment, return or suspension. c) informing the customer. d) Obtaining authorization |
– Actions will vary based on the nature of the nonconforming output such as notifying the customer when a safety or functionality issue is determined, versus a minor issue that is determined during production that can be corrected before delivery.
– Different ways to deal with NC products: Correcting- determining that the wrong meal has been prepared and providing the correct one before delivery. Segregating: Type of physical label or location Informing customer: Recall, suspension or withdrawal of affected parts, reprocessing -Nonconformance detected after delivery: An example might involve an airline providing assistance, food and/or accommodation as a result of a flight delay, until the flight can depart or until the passenger has been rebooked on another flight.
|
7 | 9.1.2: Customer Satisfaction | The organization shall monitor customers’ perceptions of the degree to which their needs and
expectations have been fulfilled. Determine the methods for obtaining, monitoring & reviewing this information. |
– Organizations will need to determine the method(s) to use, depending on the nature of their operations
– Determine the customers for taking customer satisfaction feedback and how it will monitor the information – Determine the degree of customer satisfaction after the results are analysed and evaluated and take action – Input to management review to improve customer satisfaction |
8 | 9.2: Internal Audit | -shall conduct internal audits at planned intervals
– conforms to: 2) The requirements of this International Standard effectively implemented and maintained |
– impartial view
– Audit methods should include direct observation of the process, interviews with relevant persons, examination of internal procedures, drawings, specifications, standards; customer requirements; and statutory and regulatory requirements. – where the organization has multiple sites, set up an audit programme for each specific location – The audit programme to indicate the frequency of conducting audits (e.g., monthly, quarterly, annually). – Criteria to plan the audit include importance of the processes, managerial priorities, performance of the processes, changes affecting the organization, results from previous audits, trends in customer complaints, statutory and regulatory issues -For a smaller organization, the person can audit their work but results reviewed by a peer or a manager, to ensure results are impartial – obtaining resources from an external provider like an external auditor, or another organization – to conduct combined audits to reduce redundancy. – Audit results include audit reports, evidence of corrections or corrective actions taken (e.g., training, updated documented information). |
Read More: http://bit.ly/VariableAttributeControlChart
Conclusion:
Adoption of ISO standards is strictly voluntary. This document has been developed to assist users in applying the quality management system requirements of ISO 9001:2015. This document provides guidance, with a clause-by-clause correlation to Clauses 4 to 10 of ISO 9001:2015, however, it does not guide ISO 9001:2015. This document gives examples of what an organization can do, but it does not add new requirements to ISO 9001. The examples in this document are not definitive and only represent possibilities, not all of which are necessarily suitable for every organization.
Read More: http://bit.ly/SPCandMSA
References:
ISO 9001: 2015
ISO 9000:2015
ISO/TS 9002: 2016
ISO 9004: 2018
IATF 16949: 2016
Industry Experts
This is the 193rd article of this Quality Management series. Every weekend, you will find useful information that will make your Management System journey Productive. Please share it with your colleagues too.
In the words of Albert Einstein, “The important thing is never to stop questioning.” I invite you to ask anything about the above subject. Questions and answers are the lifeblood of learning, and we are all learning. I will answer all questions to the best of my ability and promise to keep personal information confidential.
Your genuine feedback and response are extremely valuable. Please suggest topics for the coming weeks.
Recent Comments