Problem Solving Technique: Step 2-Correction, Containment, Interim Action
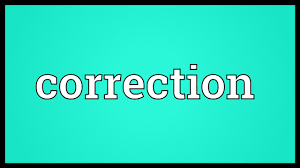
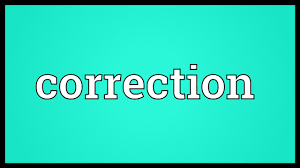
Introduction
Imagine you are going in a cab. One of the back wheel Tyre gets punctured. It is already getting late for you as you are having a business appointment with someone, shortly. The cab driver understands the situation. Rather than taking up the jockey and changing the wheel which may take some time, the driver goes to the nearby fuel station and fills the air, which is good enough to travel to the destination, thereby taking you to the destination on time. Now what he has done is provide temporary relief to his problem.
It provides temporary measures/relief to handle a situation that is providing concern to someone or something. It will act as an interim solution to a problem when we are trying to find a permanent solution.
Objective
In the problem-solving technique (8D Model), one of the important steps is to find a temporary solution to a problem till the time we can identify the root cause and can take adequate corrective action. There is different type of temporary solutions which includes Correction, Containment Action and Interim Action.
Definitions (ISO 9000: 2015)
Complaint (clause 3.9.3): Expression of dissatisfaction made to an organization related to its product or service or the complaints handling process itself where a response or resolution is explicitly or implicitly expected.
Complainant (clause 3.1; ISO 10001: 2018): Person, organization or their representative making a complaint.
Corrective Action (Cl 3.12.2): Action to eliminate the cause of nonconformity and to prevent reoccurrence.
Correction (Cl 3.12.3): Action to eliminate a detected nonconformity
Detailed Information
The following are the 7 key steps for problem-solving.
- Define the Problem
- Correction, Containment, Interim Action
- Root Cause Analysis: 3 Layered 5 Why Analysis (3L5Y), Ishikawa Diagram, PDCA
- Implementation of Corrective Action
- Effectiveness Evaluation
- Horizontal Deployment
- Documentation, Lesson Learned and Promotion of Awareness
Read More: https://bit.ly/ProblemSolvingTechnique
There can be 5 possible actions that can be taken for any material/product which is rejected internally or externally. They are
- Segregation: Containment
- Rework: Correction
- Repair: Correction
- Use as it is (Concession): Interim Action
- Scrap
Correction:
-‘Action to eliminate a detected nonconformity.’
-not a corrective action
-simply corrects the non-conformity
-does not address the cause of the problem.
Example:
- In the moulding process, if the flash is coming in the moulded component which is not desired, we may add a process to cut the flash till the time we could find a root cause of the problem and can take action on the cause so that flash (nonconformity) can be eliminated.
- You are at the office, busy with some important work and start feeling severe headache. The immediate action can be to take medicine so that the pain can be relieved so and you can finish the important work.
- You are in the maintenance process and get a complaint that a pipe is leaking. You can put an adhesive/sealant around the leak area to control the leakage.
Containment: It is immediate action to prevent the further use or distribution of non-conforming material. Containment usually consists of identifying the status of all affected material and quarantining non-conforming material to prevent further use (typically for a part or material) or distribution (typically for finished products). The containment action can be taken at the supplier end, sub-supplier end, organization, warehouse, transit warehouse, customer end, dealer end etc.
Example:
- If you receive a customer complaint about a flash in the moulded component, the immediate containment action could include
- Material ready for despatch
- Material kept at the customer end
- The material in transit to the customer
- Material kept at the assembly area for final assembly
- Moulding process where flash is generated
- You are in the maintenance process and get a complaint that a pipe is leaking. Being a process plant, it is not possible to stop the production and repair the pipeline. You can keep a bucket below the leaking pipeline so that leakage can be contained or additional drain arrangements can be made for the leaked water.
- If a complaint is received from the customer that the bulb in the headlamp is not working, the containment action can include bulbs at the supplier end, in transit to the organization, lamps fitted in the in-process and finished product at the organization end, lamps kept in the transit warehouse or at the customer end.
Interim Action: are a “first aid” that protects the customer from the problem until we define the root cause and implement permanent corrective actions.
In some cases, the interim action may be the same as or similar to the emergency response action. However, an emergency response action is implemented with minimal supporting data. An interim provides more opportunity for investigation.
Example:
- In the moulding process, if the flash is coming in the moulded component. To control the process, maybe the process engineer can review the process parameter like temperature, time, pressure etc. and can make some modifications to them and after a few trials, if the flash is controlled, the revised process parameters can be frozen for the time being till we can validate the process and can find the root cause of the problem.
- You are at the office, busy with some important work and start feeling severe headache. The interim actions could be to reduce the brightness of your laptop, take a frequent break from the work, maybe a strong cup of tea/coffee, wash your eyes with fresh water, etc.
- You are in the maintenance process and get a complaint that a pipe is leaking. You can reduce the water pressure so that the pressure on the cracked pipe can be reduced and leakage can be managed or an alternate temporary pipeline can be used.
Read More: https://bit.ly/Step1DefineProblem
Industry Challenges:
- How often, correction, containment, or interim actions are documented for reference for further review?
- How often the customer and other related stakeholders like suppliers are communicated by these actions?
- How often correction/Interim action becomes permanent action rather than going for the detailed root cause analysis and finding the proper corrective action?
References:
IATF 16949: 2016
ISO 9001: 2015
ISO 9000: 2015
ISO 18238: 2015: Space Systems-Closed loop problem-solving management
OEM Supplier Manual
CQI 20: Aug 2018, 2nd Edition (Effective Problem Solving Guide)
Industry Experts
This is the 142nd article of this Quality Management series. Every weekend, you will find useful information that will make your Management System journey Productive. Please share it with your colleagues too.
In the words of Albert Einstein, “The important thing is never to stop questioning.” I invite you to ask anything about the above subject. Questions and answers are the lifeblood of learning, and we are all learning. I will answer all questions to the best of my ability and promise to keep personal information confidential.
Your genuine feedback and response are extremely valuable. Please suggest topics for the coming weeks.
Recent Comments