Difference Between VA and VE
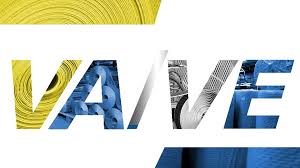
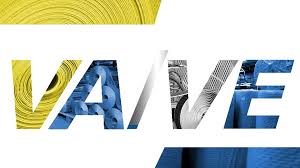
“I do not mind the difference of opinion. I do mind hate.” ― Unknown
Introduction
What is the difference between illusion and reality? The illusion is an instance of a wrong or misinterpreted perception of sensory experience. While reality is the state of things as they exist like we can see, feel or touch someone. Many times what is considered reality is considered to be Maya which we think is real but actually, it is not!
Read More: http://bit.ly/VideoAuditandInspection
Content: VA vs VE
- What is Value Analysis
- What is Value Engineering
- What is the Meaning of Value, Function and Cost?
- Key Differences
- Conclusion
Objective
Cost saving, process improvement and value enhancement in the product/process are some of the key factors to survive and sustain in the existing market. Organizations are using different tools and techniques in a structured and unstructured manner to minimize cost, improving productivity and delivery performance. Value Analysis (VA) and Value Engineering (VE) are two powerful and systematic methodologies to improve the efficiency and effectiveness of the manufacturing processes and finished product.
Once you read this blog, you will understand, what is Value Analysis, what is Value Engineering, the meaning of value, function and cost, the difference between VA & VE and how to effectively utilize them in the organization.
Read More: https://bit.ly/DifferenceOldNewFMEA
Definition: IATF 16949: 2016 (Cl 3.0)
Trade-off Curves: Tool to understand and communicate the relationship of various design characteristics of a product to each other; a product’s performance on one characteristic is mapped on the Y-axis and another on the X-axis. Then a curve is plotted to illustrate product performance relative to the two characteristics.
Trade-off Process: Methodology of developing and using trade-off curves for products and their performance characteristics that establish the customer, technical, and economic relationship between design alternatives
Design for Six Sigma (DFSS): Systematic methodology, tools and techniques with the aim of being a robust design of products or processes that meets customer expectations and can be produced at a six-sigma quality level
Design for Manufacturing (DFM): Integration of product design and process planning to design a product that is easily and economically manufactured
Design for Manufacturing and Assembly (DFMA): Combination of two methodologies: Design for Manufacture (DFM), which is the process of optimizing the design to be easier to produce, have higher throughput, and improved quality; and Design for Assembly (DFA), which is the optimization of the design to reduce risk of error, lowering costs, and making it easier to assemble
Read More: https://bit.ly/DiffVisionMission
Detailed Information
To survive and thrive in these challenging times, organizations can’t simply carry on developing, and manufacturing products in the same traditional way. They need to understand exactly where the unnecessary costs and wastages lie in their products & processes and eliminate/reduce them. The organization also needs the tools to find these economical solutions in the most creative and innovative ways possible like line balancing and manpower optimization.
If implemented appropriately (by focusing on 4M: Man, Machine, Material, Method), VA/VE projects can generate spectacular cost savings through smart material substitution and process optimization, making products more competitive and commercially attractive for the customer. The challenge for many organizations, though, is finding the priority and intelligence to develop the VA/VE processes that will leverage its benefits across the product life cycle.
Read More: https://bit.ly/JigsFixtures
What is VA (Value Analysis)?
Value Analysis (VA) is concerned with existing products and processes. It involves a current product/process being analyzed and evaluated by a team, to reduce costs, improve product function or both. Value Analysis exercises use a plan that step-by-step, methodically evaluates the product/process in a range of areas (by focusing on 4M: Man, Machine, Material, Method). These include costs, function, alternative components and design aspects such as ease of manufacture and assembly. In the automotive sector, one of the key clauses in the purchase order is related to cost reduction per year (say 1%)
For Example, Value Analysis of a wall clock will involve applying different methods to break down a wall clock’s functions and the cost involved at various stages to bring in those functions. Finally, the team will analyze the functions of the wall clock for customers, which will be to see the time and add to the beauty of their homes.
A classification between necessary and unnecessary functions will become possible based on function analysis. As a result, the business can achieve cost reduction by eliminating unnecessary functions that add to the cost but neither improve quality nor enhance customer satisfaction.
Read More: http://bit.ly/SPCandMSA
What is VE (Value Engineering)?
Value Engineering (VE) is concerned with new products. It is applied during product development. The focus is on reducing costs, improving function or both, by way of teamwork-based product evaluation and analysis. This takes place before any capital is invested in tooling, plant or equipment by focusing on 4M: Man, Machine, Material, and Method.
The main elements of the new product are identified, the functions of each element are analyzed, and areas of avoidable costs are discovered. The VE team (cross-functional) then brainstorms, develops, and evaluates alternative innovative solutions. The top alternatives are vetted further based on their potential for reducing cost without compromising quality or functionality.
For Example: In the assembly process, if the organization is using different sizes of screws (M4, M5, M6, M7, M8, M9, M10) during the product assembly, can the screws be Standardised into one or 2 categories like M6 and M8 so that inventory, bits, suppliers, storage etc. can be rationalized.
Read More: http://bit.ly/CommonSpecialCause
What is the Meaning of Value, Function and Cost?
Value = What the product is worth to the customer
Function = Properties and qualities of the product
Cost= Cost of goods sold
Difference Between VA and VE
Both VA and VE have some commonalities too like improving productivity, reducing human effort, reducing error due to human endurance, facilitating interchangeability and minimizing rejection.
Some of the key differences are as follows.
S.No. | VA (Value Analysis) | VE (Value Engineering) |
1 | Value Analysis is a cost-reduction technique applied to the existing product to enhance its worth. | Value Engineering is a technique used before the product gets approval during the development process. |
2 | Remedial Process | Preventive Process |
3 | After the product is introduced. Example: Alternate material like forging instead of machining | At the design stage. Example: Use of high tensile and impact strength CRCA sheet with low thickness |
4 | To get better optimized commercial output | To get better engineering results |
5 | Elimination of unnecessary costs. Value Analysis focuses on identifying and eliminating non-value-added features and costs. Example: 200% Inspection due to customer complaint | Prevention of unnecessary costs. Value Engineering focuses on identifying and implementing new and improved features and functions. Example: Vehicle life – 15 years |
6 | Value Analysis is more likely to have a direct impact on cost reduction | Value Engineering is more likely to have an impact on improving overall performance and customer value |
Read More: http://bit.ly/VariableAttributeControlChart
Conclusion
Though used as synonyms, the difference between value analysis and value engineering lies in the fact that the VE is concerned with improvement in the value of the product during the product development process. While VA takes place after the introduction of the product. Although the process of product optimization is virtually the same in both cases. In addition, the main objective of these techniques is to attain equivalent or better performance at a lower cost albeit without sacrificing the functional or quality requirements.
Read More: https://bit.ly/DifferenceCrandCSR
References:
ISO 9001: 2015
ISO 9002: 2016
ISO 9004: 2018
IATF 16949: 2016
Industry Experts
This is the 186th article of this Quality Management series. Every weekend, you will find useful information that will make your Management System journey Productive. Please share it with your colleagues too.
In the words of Albert Einstein, “The important thing is never to stop questioning.” I invite you to ask anything about the above subject. Questions and answers are the lifeblood of learning, and we are all learning. I will answer all questions to the best of my ability and promise to keep personal information confidential.
Your genuine feedback and response are extremely valuable. Please suggest topics for the coming weeks.
Recent Comments