What is the Difference between Product Audit and Layout Inspection?
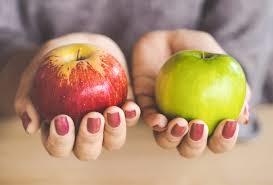
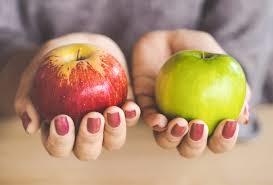
Strength lies in differences and not in similarity: Stephen Covey
Introduction
Do we know the difference between Uttarayan (Summer Solstice) and Dakshinayan (Winter Solstice)? Do we know who rotates around whom (Earth, Sun and Moon)? Do we know who is more powerful in the relationship (Husband or Wife)? Even though there are distinct differences but often we fail to realize it!
Objective
Product Audit & Layout Inspection have distinct purposes. Both are important for the effective implementation of the management system & quality of products manufactured in the organization. Although the result is to fulfil customer requirements, there are few key dissimilarities between the two. Let us understand it more.
Definitions: ISO 9000: 2015
Inspection (Cl 3.11.7): Determination of conformity to the specified requirement.
Audit (Cl 3.13.1): Systematic, independent and documented process for obtaining objective evidence and evaluating it objectively to determine the extent to which audit criteria are fulfilled
Detailed Information
In an organization, Audit and Inspection are conducted at different stages of the manufacturing process. The key objective is to ensure that product and services can fulfil the organization and relevant interested parties’ requirements (like a customer).
Before going ahead with the key difference between product audit and layout inspection, let us first understand their meaning and the key difference between audit & inspection.
What is Product Audit (IATF Clause 9.2.2.4)?
An examination of a particular product to evaluate whether it conforms to intended requirements (as per control plan).
Some of the key objectives are
are all dimensions/specifications correct?
if customer requirements are being followed?
is it in the proper box/container and properly labelled?
is all paperwork completed properly?
It helps to improve quality, increase profitability, enhance customer satisfaction and loyalty.
What is layout inspection (IATF Clause 8.6.2)?
It is the complete measurement of all part dimensions shown on the design record and functional verification to applicable material and performance standard.
A layout inspection may be required by some customers for all products at a defined frequency (annually) as per customer approved control plan. If not, the organization can also define the frequency.
Its basic purpose would be to check if everything is as per plan, and if in case any modifications are required, the same can be updated.
Similarity between Product Audit and Layout Inspection:
- Both are periodically planned
- Both may be done as per customer-defined frequency and guidelines
- Both are done by a competent person
Key Difference between Audit & Inspection
S.No. | Audit | Inspection |
1 | About the Past | About the Present |
2 | Checking how things are done | Doing something |
3 | Strength and Weakness | Fulfilment of specification |
4 | Sampling basis only | Can be sampling or 100% as per requirement |
5 | The 2-way process which results in improvement (Auditor & Auditee) | One-way process |
Key difference between Product Audit and Layout Inspection:
S.No. | Product Audit | Layout Inspection |
1 | About the Past | About the Present |
About Validation (fulfilment of the intended requirement) | about Verification (fulfilment of the specified requirement) | |
No inspection done but checked whether everything is done as per requirement or not | We measure the dimension as specified in the product drawing. | |
2 | We pick up Control plan and check whether product-related characteristics are monitored as per the requirement of the control plan or not | We pick up product drawing and do the measurement |
3 | Sampling is done at different stages of the manufacturing | No sampling is done for the dimensions or functional requirements |
4 | Conducted at different stages of the manufacturing including packaging and labelling | Done for the finished product only |
5 | Compliance of the Quality Management System for the product since the last audit like trends of statistical studies, implementation of sampling plan | Verifying the status of the product at that particular time as per the specification of all cavities / all suppliers / different assembly lines
|
6 | To verify whether the organization will be able to deliver the quality products consistently and what needs to be done to strengthen it further. | About checking the trend of dimensions since the last few inspections and judge whether these dimensions will be within specification by the next layout. |
7 | Sometimes customers conduct Product audit at Organization end | The customer never perform layout inspection but demand organization to submit the layout inspection report |
Present Challenges:
- How often qualified Internal Auditors are clear about the difference between Product Audit & Layout Inspection?
- How often Customer to the organization is clear about the difference between Product Audit & Layout Inspection?
- How often the product audit report is different from routine product inspection report?
- Inspection is done every day but layout inspection is done once in 3 / 6 / 12 months. What is the key significance of layout inspection?
References:
IATF 16949: 2016
ISO 9000: 2015
This is the 91st article of this Quality Management series. Every weekend, you will find useful information that will make your Management System journey Productive. Please share it with your colleagues too.
Your genuine feedback and response are extremely valuable. Please suggest topics for the coming weeks.
So good Sir, It cleared all doubt
Thanks Raj