Supplemental FMEA for Monitoring and System Response (FMEA-MSR) – 1st Edition: 2019 – AIAG/VDA Handbook
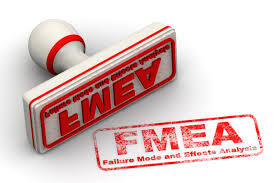
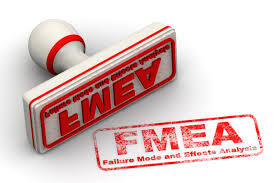
Put your heart, mind and soul into even your smallest acts. This is the secret of the success: Swami Sivananda
Introduction
Although the students study in the school still need additional support for in-depth education. The tuitions play an important role in filling that gap. These days many online programs also supplement the knowledge for the students. The role of these additional classes is to bridge the gaps which may be additionally needed.
Objective
FMEA-MSRs are added as a new, supplementary form of FMEAs with the 2019 version of the AIAG-VDA FMEA Handbook. FMEAs for Monitoring and System Response, or FMEA-MSRs, supplement DFMEAs and consider how systems can fail while being used by the customer.
Detailed Information
FMEA (Failure Mode & Effect Analysis) is a team-oriented, systematic, qualitative and analytical method to identify, analyse and mitigate the technical risks related to the ‘product and manufacturing process design.
The FMEA is the ‘Before the Event’ and not the ‘After the Event’ exercise.
The effectiveness of the FMEA can be gauged from the improvement in COQ (Cost of Quality) and COPQ (Cost of Poor Quality)
FMEA-MSRs intend to validate that diagnostic monitoring and the corresponding system responses work as they are intended.
What is an FMEA-MSR?
- An FMEA-MSR is intended to help maintain a safe state (i.e. safety) or state of regulatory (i.e. environmental) compliance during customer operation throughout the useful life of the product.
- It analyzes potential failures that may occur under normal operating conditions and their corresponding effect on the system.
- A key focus of the analysis is to determine if the system (or the end-user) detects an error when a failure does occur and then, as important, what happens next.
Why is an FMEA-MSR needed?
- FMEA-MSRs have been introduced to ensure safety goals (as required by ISO 26262) have been fully considered and are met.
- ISO 26262 defines functional safety for (automotive) equipment that applies to the lifecycle of electronic and electrical safety-related systems.
- An FMEA-MSR incorporates Functional Safety Concepts and ASIL’s (Automotive Safety Integrity Levels, an automotive-specific risk-based classification of safety goals) to the analysis of the design.
When is an FMEA-MSR used?
- An FMEA-MSR is most often used as a supplement to a DFMEA, not every design warrants a corresponding FMEA-MSR.
- If a design does not contain active or passive monitoring and response components, there is no need to conduct an FMEA-MSR.
- While DFMEAs focus on detection (and prevention) of potential failures, FMEA-MSRs focus on the efficacy of the monitoring system.
- It is often useful to define the scope to be studied in conjunction with the customer.
- Example: ECU, IoT, Mechatronics
Example:
We all have been experiencing MSR in our day-to-day life but somehow not recognizing its presence. Let me quote some examples from Automotives. We all use brakes in our cars. As of today, we normally come to know of worn-out brake pads only when we feel that it takes a longer distance for a vehicle to stop. Even when 60-70 percent of people ignore this failure and continue to use the worn-out brake pads. And then 0.05% people realize this problem when they meet an accident.
Now let us talk as to where MSR comes in. Now perceive that if had some sensor fitted in the brake pads when cautions the driver with an audio message at 70% (the unsafe zone) of brake pads wear that “Hello friend, you are now riding weaker brakes and you have another 500Km to drive when your vehicle will be made non-operable, So better take your vehicle to a service shop and get the pads replaced. In emergency still, you have an option to over-ride this warning for another 200KM”.
Now in which process can such an alert and safety system can be ensured? Not Process Design since at process design, people do what is designed at Product Design. So the obvious answer to your question is “MSR applies only to Product Design”. There are numerous other examples of MSR but ending up only with visual displays. Some of them are, Seat belt not worn, Engine overheated warning, low Engine oil warning, battery not charging warning, lower fuel warning etc.
FMEA-MSRs are conducted using the same basic seven-step team approach as DFMEAs. However, there are a few significant differences in how the Focus Element is defined and how risk is evaluated
Step 1 (Planning and Preparation)
5 key objectives:
- Project identification and boundaries: Hazard Analysis & Risk Assessment, Legal Requirements, CSR, BOM, Block diagram etc. The boundaries can be identified by asking the following questions
– Is there any effect harmful to the person or regulatory requirements?
– Did DFMEA identify Causes that lead to harm or regulatory compliance?
– Did DFMEA indicate that the detected Cause is to switch to a degraded operational state or inform the driver or diagnostic guidelines?
- Project plan (5T): InTent, Timing, Team, Task, Tools
- Analysis boundaries: what needs to be included and excluded
- Identification of baseline FMEA with the lesson learned
- The basis for step 2 (Structure Analysis)
Step 2 (Structure Analysis)
5 key steps:
- – Visualization of the analysis scope.
- – Structure Tree, Boundary diagram
- – Identification of design interfaces, interactions
- – Collaboration between customer and organization
- – Input for the Functional Analysis (Step 3)
- – Consists of three expanded columns whose purpose is to facilitate a thorough understanding of the process. Start with the Focus Element in the “middle column,” then identify the Process of which the Focus Element is a part and finally identify all Process Work Elements of the Focus Element.
Step 3 (Function Analysis)
7 Key Objectives:
- Visualization of the function and relationship between functions
- Functional tree/network and P-diagram
- Cascade of the customer (internal and external) functions with associated requirements
- Association of requirements or characteristics to functions
- Collaboration between engineering teams (system, safety, components)
- The basis for the 4th step (the failure analysis)
- Detailed graphical representation of the function (visualization)
Step 4 (Failure Analysis)
5 Key objectives:
- – Establishment of the failure chain
- – Identification of potential Failure Causes, Monitoring, System Response, Reduced Failure Effects
- – Identification of product failure causes using Parameter Diagram
- – Collaboration between customer and supplier
- – The basis for Risk Analysis (Step 5)
Failure Chain:
- Failure Modes (FM): It means the ways, or modes, in which something might fail.
- Failure Effect (FE): It refers to studying the consequences of those failures’ mode.
- Failure Cause (FC): A indication of why failure mode could occur
Step 5 (Risk Analysis)
7 Key Objectives:
- – Assignment of existing or planned controls and rating of failure
- – Assignment of preventive control to the failure causes
- – Assignment of detective control to the failure causes or failure modes
- – Rating for Severity, Frequency and Monitoring for each failure chain
- – Evaluation of action priority
- – Collaboration between customer and supplier related to the severity
- – The basis for the optimization step (Step 6)
Severity (S): Represents the Severity of the Failure Effect (FE)
Frequency (F): Frequency of the occurrence of the Failure Cause in a given operational situation during the intended service life of the vehicle
Monitoring (M): Detection potential of the diagnostic monitoring functions (Detection of the Failure Cause (FC), Failure Mode (FM) and/or Failure Effect (FE)
Action Priority (AP)
The key objective of ‘Action Priority’ is to choose, how to best prioritize the need for action considering Severity, Frequency and Monitoring (SFM).
Priority High (H):
- – Highest priority for review and action.
- – Either identify an appropriate action to lower frequency and/or improve monitoring control
- – Or justify and document why current controls are adequate
Priority Medium (M):
- – Medium priority for review and action.
- – Either identify an appropriate action to lower frequency and/or improve monitoring control
- – Or at the discretion of the organization, justify and document why controls are adequate
Priority Low (L):
- – Low priority for review and action.
- – Could identify actions to lower frequency and/or improve monitoring control
Step 6 (Optimization)
9 Key Objective:
- – Identification of actions necessary to reduce the risk
- – Assignment of the responsibility and target date for action implementation
- – Implementation and documentation of the action taken
- – Verifying the effectiveness of the implemented actions
- – Assessment of the risk after the action is taken (S, F, M)
- – The basis for refinement of the product requirements and prevention/detection controls
- – Collaboration between CFT and other relevant interested parties like the customer, supplier, process owner etc.
- – Optimization is effective in the following order
Component design modification to reduce the frequency (F) of the Failure Cause (FC)
Increase the Monitoring (M) ability for the Failure Cause (FC) or Failure Mode (FM)
- – Separate Prevention and detection controls
Step 7 (Results Documentation)
5 key objectives:
- Communication of the results and conclusion of the analysis
- Establish: Content of the documentation
- Documentation: Effectiveness of the actions taken and assessment of the risk after action taken
- Communication: Actions to reduce risk within organization, customer, supplier
- Record: Risk analysis, risk reduction
Present Challenges:
- How often the cross-functional team is aware of the requirements of MSR while working on DFMEA?
- How often the customer demands the preparation of MSR along with DFMEA, where applicable?
- How often the output of FMEA-MSR is discussed in the Management Review by the top management?
References:
IATF 16949: 2016
FMEA Handbook (AIAG-VDA 1st Edition June 2019)
Industry Experts
This is the 131st article of this Quality Management series. Every weekend, you will find useful information that will make your Management System journey Productive. Please share it with your colleagues too.
In the words of Albert Einstein, “The important thing is never to stop questioning.” I invite you to ask anything about the above subject. Questions and answers are the lifeblood of learning, and we are all learning. I will answer all questions to the best of my ability and promise to keep personal information confidential.
Your genuine feedback and response are extremely valuable. Please suggest topics for the coming weeks.
Recent Comments