OEE (Overall Equipment Effectiveness)
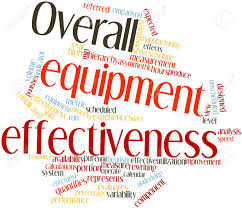
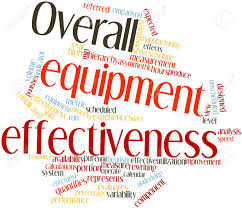
“Efficiency is doing things right; effectiveness is doing the right things.” – Peter Drucker
Introduction
For the connoisseurs of Cricket, both ‘Run rate’ and ‘playing for complete 50 overs’ is important. The run rate helps the team to build the pressure on the other team while playing for the full 50 overs not only tires the other team but also creates more opportunities to score more. The consistent performance of the team and the players also gives them an additional edge over the other team.
Objective
OEE (Overall Equipment Effectiveness) is the gold standard for measuring equipment effectiveness (sometimes, we use it to monitor manufacturing productivity too!). While looking at operations, OEE simply gives a clear and powerful view of the ability to sustain quality production or how availability (time), quality (good product) and performance (speed) interact. OEE is the roadmap for other activities such as continuous improvement, lean, six-sigma and Cost of Quality.
For any organization to run profitably, both Effectiveness & Efficiency indicators are important. OEE is an excellent indicator related to the Effectiveness of the machine. It is the single best metric for identifying losses, benchmarking progress, and improving the productivity of manufacturing equipment (i.e., eliminating waste).
Read More: https://bit.ly/PESTLEANALYSIS
Definition (ISO 9000: 2015):
Efficiency (Cl 3.7.10): Relationship between the result achieved and the resources used
Effectiveness (Cl 3.7.11): The extent to which planned activities are realized and planned results are achieved
Read More: https://bit.ly/WhatEmbeddedSoftware
Detailed Information
Overall Equipment Effectiveness[1] (OEE) is a measure of how well a manufacturing operation is utilized (facilities, time and material) compared to its full potential, during the periods when it is scheduled to run. It identifies the percentage of manufacturing time that is truly productive. An OEE of 100% means that only good parts are produced (100% quality), at the maximum speed (100% performance), and without interruption (100% availability).
In the early 1980s, Seiichi Nakajima from Japan introduced this terminology to the world. As per him, in TPM, the goal is, “The continuous improvement of OEE by engaging all those that impact on it in small group activities”.
How to set a Target for OEE?
Just like RPN (Risk Priority Number) in the FMEA manual (AIAG/VDA 1st edition), there is no target value for OEE. The objective of any organization is to have incremental improvement from its existing level, which leads to manufacturing improvement.
In IATF 16949, OEE is one of the key indicators in Clause 8.5.1.5 (TPM).
Read More: https://bit.ly/WhatisCyberSecurity
Availability is calculated as the ratio of Run Time to Planned Production Time.
- Run time is the actual time where production happened after subtracting the time of line stoppage due to Machine failure, Tool Failure, Planned changeover, Operator non-availability etc.
- Planned Production time is total production time minus planned lunch and tea breaks.
Performance: It takes into account anything that causes the manufacturing process to run at less than the maximum possible speed when it is running. Performance is the ratio of Net Run Time to Run Time.
Quality: It considers manufactured parts that do not meet quality standards, including parts that need rework. OEE Quality is similar to First Pass Yield (first-time pass without needing any rework).
Example of OEE Calculation:
Read More: https://bit.ly/DiagramTurtleDiagram
While calculating OEE, it is important to identify and improve on the possible causes of losses. Traditionally, there are 6 big losses that need the attention of supervisors & managers.
OEE and Cost of Quality (COQ) are related indicators. The “Cost of Quality” isn’t the price of creating a quality product or service. It is the cost of not creating a quality product or service. If OEE is low, it has a direct bearing on low COQ.
Read More: https://bit.ly/GeneralDataPR
5 Key Questions related to OEE
Question 1: Is it an Effectiveness or Efficiency Indicator?
Answer 1: From the name itself, it is clear that it is an Effectiveness Indicator for Machine performance.
Question 2: Should we have the same OEE target for different assembly lines producing different Products?
Answer 2: Consider that there is 2 assembly line. One line is producing only 1 product while the other is assembling 5 different products. Will it be prudent to have the same OEE target as we know that the change-over-time in line 2 will be much higher than 1 which will result in low availability time, resulting in lower OEE? So, it is pertinent to have different OEE targets for dissimilar processes in the same organization.
Question 3: Should we benchmark our OEE target from other similar industries?
Answer 3: When we should not have a similar OEE target for dissimilar processes in the same organization, will it be advisable to benchmark our OEE target from other industries? The obvious answer should be NO.
Read More: https://bit.ly/FaultTreeAnalysisFTA
Question 4: Is it an indicator related to Equipment Performance or Manufacturing Productivity?
Answer 4: Equipment Performance. That is why it is an indicator specified in clause 8.5.1.5 (Total Productive Maintenance). It is a performance of how during the new product development process, selection of machine was conducted and how it is maintained after purchasing.
Question 5: Should we have a target only for OEE% or also for Availability, Performance and Quality?
Answer 5: There should be a specific target for OEE, Availability, Performance and Quality. Refer to the below example.
Target | Case 1 | Case 2 | Case 3 | |
Availability | 95% | 100% | 100% | 90.25% |
Performance | 2% Losses | 100% | 90.25% | 100% |
Quality | 1000 ppm | 90.25% | 100% | 100% |
OEE% | 90% | 90.25 | 90.25 | 90.25 |
Steps to Improve OEE%:
- Effective use of cross-functional team approach during machine selection during new product development
- Involvement of maintenance personnel during the selection of machine
- Linking machine selection with customer/organization-defined QCD parameters (Quality, Cost, Delivery). Like during the new development process, the customer targets could be 100% Delivery, 200 ppm quality, Cost: Considering 5% overheads. while selecting a new CNC machine, we should consider these parameters.
- Monitoring and improving Machine ‘Availability’. Somebody has rightly said, “Time is Money“. Machine availability means managing unplanned breakdown of machines and tooling, Tool change over time etc. There are many popular methodologies to improve machine availability. Like, there should be clarity, on how to calculate Set up time. The best policy is “Set up is the time between the last OK product to the First OK product after the next job setup“.
- Another important technique for improving ‘Availability’ is by improving set up time is SMED (Single Minute Exchange of Dies).
Read More: https://bit.ly/DiagramSIPOCDiagram
Industry Challenges:
- The real challenge for any organization is not to improve their OEE but to improve the quality of data collection. Whether the data for OEE genuine?
- In how many organizations, there is a serious analysis of OEE?
- In how many organizations OEE is calculated and presented to Management without understanding its intent of it?
Read More: https://bit.ly/SWOTAnalysisEV
References:
ISO 9001: 2015
IATF 16949: 2016
IATF 16949: 2016, Sanctioned Interpretation & FAQ
Industry Experts
This is the 159th article of this Quality Management series. Every weekend, you will find useful information that will make your Management System journey Productive. Please share it with your colleagues too.
In the words of Albert Einstein, “The important thing is never to stop questioning.” I invite you to ask anything about the above subject. Questions and answers are the lifeblood of learning, and we are all learning. I will answer all questions to the best of my ability and promise to keep personal information confidential.
Your genuine feedback and response are extremely valuable. Please suggest topics for the coming weeks.
Recent Comments