KAIZEN (Continuous Improvement)
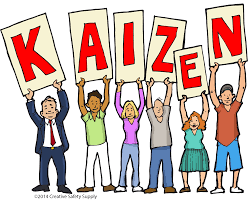
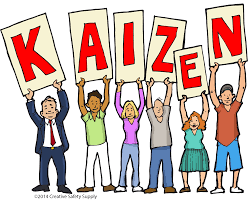
“True life is lived when tiny changes occur.”– Leo Tolstoy
Introduction
When the child is born and the physical growth happens, as parents we find it difficult to feel that but an outsider can easily detect the physical growth in the child. Similarly, daylighting gradually changes every day (increase and decrease) and we could only realize it when there is a distinct change in daylight. This is the power of gradual but continuous change.
Read More: https://bit.ly/OnJobTrainingOJT
Objective
Kaizen has its origins in post-World War II Japanese quality circles. These circles or groups of workers focused on preventing defects at Toyota. They were developed partly in response to American management and productivity consultants who visited the country, especially W. Edwards Deming, who argued that quality control should be put more directly in the hands of line workers. Kaizen was brought to the West and popularized by Masaaki Imai via his book Kaizen: The Key to Japan’s Competitive Success in 1986.
This article will cover what is Kaizen, the goal of Kaizen, the Five fundamental Kaizen Principles, the Seven step Kaizen cycle for continuous improvement, why it important and the possible benefits. Once you read this blog, you will understand the true meaning of Kaizen and how to implement it at your workplace successfully.
Read More: https://bit.ly/DOJOCentre
Definition:
Competence (ISO 9000: 2015, Cl 3.10.4): Ability to apply knowledge and skills to achieve intended results
Skill (ISO 30401: 2018, Cl 3.30): Learned capacity to perform a task to a specified expectation
Knowledge (ISO 30401: 2018, Cl 3.25): Human or organizational asset enabling effective decisions and actions in the context
Read More: https://bit.ly/OrganizationKnowledge
Detailed Information
What is Kaizen?
Kaizen is an approach to creating continuous improvement based on the idea that small, ongoing positive changes can reap significant improvements.
As per a new definition of Kaizen by Masaki Imai, it is Everyday Improvement, Everybody Improvement and Everywhere Improvement.
Everyday: We must improve every day. Say we completed a 6 Sigma project 3 months and we have not done any improvement since then, it means, we are missing the essence of improvement.
Everybody: Kaizen is not only for the shop floor operator but for everyone in the organization.
Everywhere: Kaizen is not only for the manufacturing process but also for Marketing, New development, Quality, Purchase, and Finance process too.
Read More: https://bit.ly/ROI-Training
The successful use of Kaizen depends on gaining support across the organization and from the Top-Down approach.
Kaizen focuses on group activity (quality circles) and promotes teamwork and team spirit; however, it also recognizes individual contributions. It emphasizes the engagement of each worker in the concept and vision of the company so that employees will identify themselves with the organization, its culture and its objectives.
The important aspects of Kaizen are:
- What is wrong? not who is wrong?
- How to eliminate waste (Muda)
- How to decrease Cost of Quality (COQ)
Read More: https://bit.ly/TraningNeedIdentification
Misconception about Kaizen:
The general understanding in the industry is that Kaizen is a standalone activity wherein a worker will suggest an improvement activity in their area. Once the improvement activity is implemented, it will be recorded on a sheet (Before and After) for documentation purposes.
Apart from that, another misconception is that Kaizen is ONLY for the worker but it is not correct. The kaizen should initiate from the top of the organization. Moreover, it is not only for full-time employees but also for part-time/contract employees too.
Kaizen is a concept for gradual improvement in any part of the organization. Kaizen is an umbrella that encompasses all the initiatives in the organization like Quality Circle, TPM, Kanban etc.
Kaizen is a philosophy in the Lean system that focuses both on the process and the
Results. Although Kaizen is more concerned with the process rather than the result. As the results will automatically come when we focus on the process.
Kaizen promotes small improvements, not big improvements to make rapid change. This mindset helps enterprises achieve their goals through gradual improvements from solving small problems to creating bigger improvements. Meanwhile, it is a long-term process of human development; and it is a continuous process to enhance human abilities.
Read More: https://bit.ly/TrainerCompetency
Five Fundamental Kaizen Principles:
The 5 principles are:
- Know your Customer
- Let it Flow
- Go to Gemba
- Empower People
- Be Transparent.
The implementation of those 5 principles in any organization is fundamentally important for a successful Continuous Improvement culture and to mark a turning point in the progression of quality, productivity, and labour-management relations.
Kaizen emphasizes Problem awareness and provides clues for identifying problems. It is a problem-solving tool. Kaizen also needs standardization after implementation. Investing in Kaizen means investing in People.
Read More: https://bit.ly/Kirkpatrick4LevelModel
Conventional wisdom:
- Higher quality leads to higher cost
- Larger lots lead to lower cost
- Workers do not need to be taken into account
Japanese revolution:
- Higher quality leads to lower cost
- Shorter lots lead to lower cost
- A thinking worker is a productive worker
But a suggestion for Kaizen should be bottoms-up as the best specific suggestion for improvement should generally come from people close to the problem. The Kaizen can be initiated at three different levels.
- Management oriented kaizen
- Group-oriented kaizen
- Individually oriented kaizen
Kaizen is based on the belief that everything can be improved, and nothing is the status quo.
Read More: https://bit.ly/CompetencyMapping1
Kaizen Cycle for Continuous Improvement
Kaizen can be implemented in a seven-step cycle to create an environment based on continuous improvement. This systematic method includes the following steps:
Get Employees Involved: Seek the involvement of employees, including getting their help in identifying chronic problems. Often, this is organized as specific groups of individuals charged with gathering and relaying information from a wider group of employees.
- Find Problems: Using widespread feedback from all employees across the organization, gather a list of problems and potential opportunities. Create a list if there are many issues. The issues can be related to PQCDSM (Productivity, Quality, Cost, Delivery, Safety, Morale)
- Create a Solution: The person who is working in a particular process (Finance, Sales, New Development, Quality, Stores, Maintenance) can identify the problem and the possible solution too. Encourage employees to offer creative solutions, with all manner of ideas encouraged. Pick the best possible option or options from the ideas presented.
- Test the Solution: Depending upon the criticality of the possible solution, implement the winning solution chosen above, with everyone participating in the discussion. Create a pilot program or take other small steps to test out the solution.
- Analyze the Results: At periodic intervals, review the result of the implemented action with the process owner and determine the performance.
- Adopt the Solution: If results are positive, horizontally deploy the solution throughout the organization.
- Repeat: These seven steps should be repeated on an ongoing basis, with new solutions tested where appropriate or new lists of problems identified.
Read More: https://bit.ly/CompetencyRequirement
Benefits of Kaizen (Improvement)
- lower defects
- eliminate waste
- boost productivity
- empowers the employees
- promote innovation.
Read More: https://bit.ly/EmployeeSatisfaction1
Industry Challenges:
- How often the top management of the organization is consistently involved in the Kaizen process?
- How often it is understood that Kaizen is only for the shop floor and not for all the processes in the organization?
- How often Kaizen is a continuous activity and not a standalone activity?
Read More: https://bit.ly/DifferenceCoachingMentoring
References:
ISO 9001: 2015
ISO 9002: 2016
ISO 9004: 2018
IATF 16949: 2016
Industry Experts
This is the 172nd article of this Quality Management series. Every weekend, you will find useful information that will make your Management System journey Productive. Please share it with your colleagues too.
In the words of Albert Einstein, “The important thing is never to stop questioning.” I invite you to ask anything about the above subject. Questions and answers are the lifeblood of learning, and we are all learning. I will answer all questions to the best of my ability and promise to keep personal information confidential.
Your genuine feedback and response are extremely valuable. Please suggest topics for the coming weeks.
Recent Comments