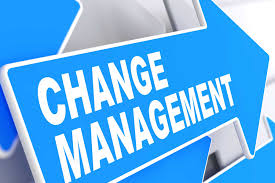
Engineering Change Management (Part 7 of 8)
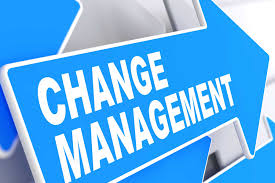
“Slowness to change usually means fear of the new.” – Philip Crosby“
Introduction
Change is part and parcel of our life. Some changes are planned like a change of business, job, shifting to another city or country, the birth of a baby etc. But there are many which are not planned and are thrown on us like COVID-19, demonetization etc. In both the situation, we have to adapt ourselves to the new reality, at times with some difficulty.
Objective
The key objective of the change management process is to understand the need and expectation of the customer & relevant interested parties and make the changes in such a way that customer requirement is taken care and satisfaction of all the relevant interested parties including the organization is ensured.
Definitions
As per ISO 9000: 2015, clause 3.0, following are some of the key definitions related to the design process
Configuration Management (Clause 3.3.9): It is coordinated activities to direct and control configuration.
Note: establish and maintain control of a product or service and its product configuration information throughout the life cycle of the product.
Change Control (Clause 3.3.10): Activities for control of the output after formal approval of its product configuration information.
Customer Specific Requirements (CSR) of IATF subscribing OEM
FCA, USA & Italy | SQ00012 Forever Requirements |
Renault | As per ANPQP Chapter 9 |
GM | Written Customer Approval or waiver, Trial Runs |
Daimler | MBST 13 / 18, Section 4 |
VW | As per Formel-Q-Konkret Chapter 5, VW 01155 |
Detailed Information
As per ISO 9001 and IATF 16949, Clause 7.5.3.2.2 and 8.3.6, following are some of the key requirement for the Change Management Process. All these requirements should be documented (procedure) systematically for easy understanding and effective implementation.
- Who can propose change?
- Customer
- Organization
- Supplier
- Any other relevant interested party
- When change can happen?
- During the development process
- During/After PPAP Lot (Production Part Approval Process)
- After mass production started
- To enhance customer satisfaction
- Any change at supply chain
- What can be Possible changes?
- Drawing change after DFMEA review
- Drawing / Process change after PFMEA review
- Changes after Verification study
- Changes after Validation Study
- Any change in 5M (Man, Machine, Material, Method, Measurement), Environment at organization and supplier chain
- What needs to be reviewed after the change? The review should be completed within 10 days from the date of receipt of engineering change.
- Fit
- Form
- Function
- Performance
- Durability
- Impact on other parts
- Impact on the existing stock (supplier, organization, transit, Customer)
- How to ensure the effectiveness of change?
- Validation against customer requirement
- Approved internally by the organization
- Tested and validated on a sample lot before mass production implementation
- Effective communication to the customer and all relevant interested parties like sub-suppliers
- Documented Information:
- Design and development changes
- Results of reviews
- Authorization of the changes
- Actions taken to prevent adverse impacts
- The actual date of implementation of each proposed change
- Waiver if needed
- Special control for embedded software:
- Document revision number for Hardware
- Document revision number of Software
Example: If an Engineering Change results in changing dimension of a component from 5.5 mm to 5.7 mm. The possible documents which may need review & change include
- Product drawing
- Component drawing
All relevant PPAP documents including following
- DFMEA
- Process Flow Chart
- PFMEA
- Control Plan
- Work Instruction
- Communication to Supplier if purchased
- Changes in Supplier Control plan & Work instruction
- In-process Inspection sheet
- Pre-despatch Inspection sheet
- SPC chart & comments (if Special Characteristic)
- MSA Study (if it has resulted in a change in measuring instrument)
- May be few more….
Benefits to Organization:
- Systematic and effective change management
- Cost-saving when changes are implemented systematically and on time
- Enhanced satisfaction for the customer and all relevant interested parties
Present Challenges:
- How often Cross-Functional Team (CFT) approach is used for change management process?
- How often customer approval/waiver is taken where needed?
- How often all the relevant documents are reviewed and changed like DFMEA, PFMEA, Control Plan etc.?
- How often the customer is communicated about any 5M change at organization/supplier end?
References:
ISO 9000: 2015
ISO 9001: 2015
IATF 16949: 2016
ISO/TS 9002: 2016
This is the 80th article of this Quality Management series. Every weekend, you will find useful information that will make your Management System journey Productive. Please share it with your colleagues too.
Your genuine feedback and response are extremely valuable. Please suggest topics for the coming weeks.
It’s realy a summery of important points for change managment.
Thanks Ashwani