What is the key difference between Failure Mode, its Causes and its Effects (FMEA)?
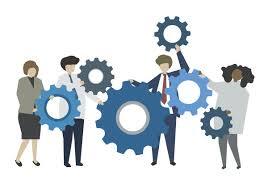
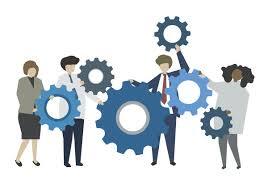
The difference between something good and something great is attention to detail: Charles R Swindoll
Introduction
What is the domino’s effect? It is a cumulative effect produced when one event sets off a chain of similar events. When the Domino’s effect is favourable, it produces positive results else the results are negative.
Objective
The FMEA is a deep dive analysis process of identifying possible internal and external failures.
The key objective of implementing the FMEA (Failure Mode and Effect Analysis) manual is to improve robustness, performance, effectiveness and efficiency of the product and manufacturing processes. By clearing understanding and identifying the Failure Chain, the organization can effectively link Failure Mode (FM) with Failure Effect (FE) and Failure Causes (FC).
Definitions
Design for Assembly (DFA): the process by which products are designed with ease of assembly considerations. (e.g., if a product contains fewer parts it will take less time to assemble. thereby reducing assembly costs)
Design for Manufacturing (DFM): integration of product design and process planning to design a product that is easily and economically manufactured
Design for Manufacturing and Assembly (DFMA): the combination of two methodologies: Design for Manufacture (DFM), which is the process of optimizing the design to be easier to produce, have higher throughput, and improved quality; and Design for Assembly (DFA), which is the optimization of the design to reduce risk of error, lowering costs and making it easier to assemble
Detailed Information
FMEA (Failure Mode & Effect Analysis) is a team-oriented, systematic, qualitative and analytical method to identify, analyse and mitigate the technical risks related to the product and manufacturing process design.
The FMEA is the ‘Before the Event’ and not the ‘After the Event’ exercise.
When FMEA is implemented effectively, it not only impacts the organization in the form of improved performance but also their bottom line (profitability).
- Failure Modes (FM): It means the ways, or modes, in which something might fail. Failures are any errors or defects, especially ones that affect the customer and can be potential or actual.
- Failure Effect (FE): It refers to studying the consequences of those failures.
- Failure Cause (FC): A indication of why failure mode could occur
One of the key inputs for the Failure Analysis is ‘Complete description of the Process Functions in Positive words’ like Drill Hole, Apply Grease.
Key objective (Product and Process Failure Analysis):
- Establishment of the failure chain
- Identification of potential Failure Effects, Failure Mode and Failure Causes for each process function
- Understanding the Failure Effect to the Customer and the supplier
Failures:
- Non-conformities
- Unintentional activity
- Unnecessary activity
- Inconsistent or partially executed task
Failure Chain:
- Failure Effect (FE)
- Failure Mode (FM)
- Failure Cause (FC)
Who is Customer:
- Internal (next process)
- External (Tier 2, Tier 1, OEM, Dealer)
- Legal bodies
- Product end-user
Basic Assumption:
- The basic design of the product is correct
- If there is a design issue, it should be communicated to the Design team
- The incoming material/part are correct
- Failure mode could occur but may not necessarily occur
Failure Effect (FE): It is the consequence of a Failure Mode (FM). Many times the OEM/Customer can also share the impact of the effect to their suppliers and sub-suppliers.
- What customer might notice or experience
- Could impact Safety
- Could impact Statutory or Regulatory requirement
Output of Failure Effect (FE): Identification of Severity Rating
- Your plant (if failure is detected internally)
- Your immediate customer to whom the product is supplied
- End-user (performance issue like poor appearance, loss of steering or brake)
Possible Questions related to Failure Effect (FE):
- Does the failure mode physically impact the next process/operator/equipment?
- Potential impact on the End-user (Link DFMEA with PFMEA)
- What would happen if the failure effect is detected before it reaches the end-user?
Failure Mode (FM): How the process could cause the product not to deliver or provide the intended function. Failure mode should be defined in the Technical Terms and not as symptoms.
Possible Inputs for Failure Mode (FM):
- Past things went wrong
- Reject report
- Scrap report
- Brainstorming by the cross-functional team
- Customer rejection
Possible categories of Failure Mode (FM): It can be at the Component level or System-level or Process level
- Loss of process function: Label missing
- Partial / Degradation of function: bar code not readable
- Unstable operation: Pass a bad part or reject a good part
- Wrong part installed: ECU flashed with the wrong software
- Overachieving process function: Surface finish too smooth
Failure Cause (FC): A indication of why failure mode could occur. The consequence of a Cause is the Failure Mode (FM).
Possibility for Failure Cause (FC): The Cause should be listed as concisely and completely as possible so that remedial efforts can be aimed at appropriate causes.
Ask possible questions related to
- Man: Setup operator, Maintenance personnel
- Machine: Robot, Moulding machine, Fixture
- Material: Machining oil, washer, Grease
- Method: How to tighten the bolt, how to clean the hopper
- Measurement: Vernier, Micrometer, Temperature gauge
- Environment: Ambient condition like heat, dust, lighting noise
How to describe Failure Cause (FC): The Failure Causes should be clear like
- Inadequate Design from functional problems
- Changes over time
- Design inadequate for the external environment (heat cold, moisture)
- End-user error or behaviour (wrong gear used, wrong fuel used)
- Software issues (Corrupted)
Right Question:
To link Failure Cause (FC) to Failure Mode (FM): Why is the Failure Mode happening?
To link Failure Effect (FE) to Failure Mode (FM): What happens in the event of the Failure Mode?
Example:
DFMEA
Function | Failure Effect (FE) | Failure Mode (FM) | Failure Cause (FC) |
Stop Vehicle on pressing the brake pedal | Vehicle Control impaired | The vehicle does not stop | Loss of hydraulic fluid from loose hydraulic line |
Regulatory non-compliance | Mechanical linkage break due to inadequate corrosion protection | ||
Master cylinder vacuum lock due to seal design |
PFMEA
Function | Failure Effect (FE) | Failure Mode (FM) | Failure Cause (FC) |
Attach seat cushion using a torque gun with 4 screws | Loose seat cushion | Fewer than 4 screws | No work instruction to specify the number of screws to be fitted |
Shipment of the customer stopped and rework | Desired number of screws not available | ||
Delay in delivery to the customer | Operator not aware of the number of screws to be fitted |
Present Challenges
- How often the organizations are clear about the interlinkage between Failure mode and its effect and causes?
- How often the CFT (Cross-Functional Team) which participates in the FMEA development are competent as per FMEA 1st edition?
- How often the top management is linking the effectiveness of FMEA with the reduction in COPQ (Cost of Poor Quality)?
- How often the recommended and pending actions from the FMEA are key inputs for the management review?
References:
IATF 16949: 2016
FMEA Handbook (AIAG-VDA 1st Edition June 2019)
Industry Experts
This is the 120th article of this Quality Management series. Every weekend, you will find useful information that will make your Management System journey Productive. Please share it with your colleagues too.
Your genuine feedback and response are extremely valuable. Please suggest topics for the coming weeks.
Very helpful to understand failure chain….thank u so much sir
Thanks Gaurav for your response.