Management Review (ISO 9001 / IATF 16949)
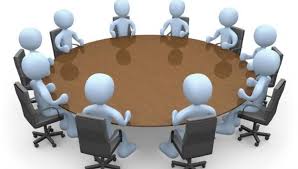
“What’s measured, improves” — Peter F. Drucker
A student periodically reviews his/her course preparation and studies accordingly. An architect reviews the construction as per approved drawing. A long-distance runner reviews their target time and runs accordingly. Families review the income & expenses regularly and plan further expenses. Similarly, an organization also periodically reviews its performance against the set target.
All management systems require a periodic review by the organization’s top management. The purpose of such a review is to evaluate if the management system is performing as intended and if it’s delivering the desired results as effectively & efficiently as possible.
Management review meeting can be a stand-alone management review or it can be a combination of different review meetings e.g. strategic planning, business planning, operations meetings, process reviews, customer requirements or functional reviews. A Management Review also ensures that all levels of management are made aware of any changes, updates, revisions, etc. to the day-to-day workings of the Management System itself.
As per ISO 9000:2015, the following are the definitions
Review (Clause 3.11.2): Determination of the suitability, adequacy or effectiveness of an object to achieve established objectives.
Top Management (Clause 3.1.1): Person or group of people who directs and controls an organization at the highest level. The top management has the power to delegate authority and provide resources within the organization.
Some of the IATF subscribing OEM have their specific requirements related to the Management Review Process.
FCA, USA
Design and development planning · Supplier QMS development · Customer satisfaction · QMS audit · Manufacturing process audit · Warranty Management
FCA, Italy
Monthly review & its availability in the SQP system; • Result of application of the Safety Characteristics Management (including audits); • Result of tickets of non-conformities opened in the SQP system, according to norm 08018; • Special notifications • Status of the product approval process •WCM development status
Ford
Monthly QOS (Quality Operating System) performance meetings. Q1 Manufacturing Site Assessment results
As per ISO 9001 & IATF 16949, clause 9.3, the organization has to conduct Management Review at planned intervals (at least once annually) to analyse the performance of its different process as per QMS. The output of the management review has to be documented and retained. The frequency of the management review is linked with the performance (risk) of the management system and customer requirement.
Following are the inputs for Management Review.
- Previous management reviews results: Any pending issue, any major decision, the effectiveness of the output of the previous meeting etc.
- Changes in external and internal issues: Status of interested parties, merger, acquisition, new product/process addition which can impact interested parties, the addition of new management system etc.
- Customer satisfaction: Data related to Quality, Delivery, Premium Freight, Special status notification, customer audit, customer survey, customer rating, the share of the business.
- Audit results (internal & customer): Status of internal audit results like System audit, Manufacturing process audit, Product audit, Customer audit.
- Nonconformities and corrective actions: Result of customer and supplier audit, customer complaints and related action plan and its closure.
- Performance of suppliers: Supplier rating based on Quality, Delivery, Premium Freight, Customer Notification, Customer audits, QMS status, Selection of a new supplier, their Financial status, dependability on suppliers etc.
- Adequacy of resources: Manpower, Machines, Infrastructure, Raw Material, Environment, Safety equipment’s etc.
- Cost of poor quality: Internal Failure cost, External failure cost, preventive cost, Appraisal cost.
- Process Effectiveness & Efficiency: OEE, production plan achievement, COQ, Inventory turnover etc.
- Product conformance: Internal Rejection, Scrap, Segregation, Rework, Temporary changes, warranty, customer complaints, customer rejection, Delivery performance etc.
- Manufacturing feasibility: Status of new product or processes under development
- Maintenance objectives: MTTR, MTBF, OEE, Breakdown hours, Power cost etc.
- Warranty performance: Rejection from Field, data for No Trouble Found (NTF)
- Customer scorecards: Data from the customer portal, monthly/quarterly report
- Potential field failures: Output of DFMEA and PFMEA and proposed actions
- Status of design and developments: As per APQP time plan, as per customer target date, tool development time, supplier selection process, tool trial dates, PPAP date etc.
- Effectiveness of actions taken to address risks and opportunities: Key Risk and opportunities
- Opportunities for improvement: What needs special focus
Following are the outputs for Management Review
1. Opportunities for improvement: Proposed actions from top management.
2. Changes to the quality management system: Change of MR, Quality Manual, the addition of another system
3. Resource needs: Additional resources proposal related to Manpower, Machines, Infrastructure, Raw Material, Environment, Safety equipment’s etc.
4. Action plan when customer performance targets are not met: Direction from top management to achieve customer performance target by providing additional resources, understanding customer requirements, meeting customer if needed etc.
Who should participate?
· Top Management like Managing Director, CEO, President
· First layer reporting to Top Management
· Process owners or anyone who is important for that meeting
How to Measure the Effectiveness of Management Review Meeting?
- Enhanced customer & employee satisfaction
- Improvement in new business generation
- Identify the strength and weaknesses of the organization
- Improved & sustained Profitability
Some question to ponder:
- How often top management actually conducts a detailed Management Review?
- Who prepares the output of Management review? Management Representative? If yes, if MR is always competent to do it?
- What is the objective of conducting Management review? Improvement in Processes or fulfilment of ISO requirements?
- How often the organization increases the frequency of Management review based on the risk related to interested parties and performance?
- If there is any measure to analyse the effectiveness of Management Review Meeting?
References:
IATF 16949:2016
ISO 9001: 2015
ISO 9000: 2015
This is the 47th article of this Quality Management series. Every weekend, you will find useful information that will make your Management System journey Productive. Please share it with your colleagues too.
Your genuine feedback and response are extremely valuable. Please suggest topics for the coming weeks.
Amazing
Good
Great Bhavya Sir
Good