Continual Improvement
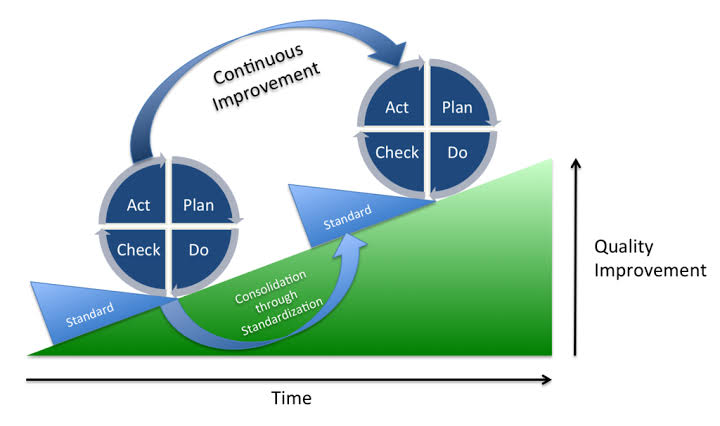
“To improve is to change, to be perfect is to change often: Winston Churchill”
Improvement is a never-ending process. We have improved our transportation system from Bullock Cart to Bicycle to 2-wheeler to 4-wheeler to Airplane. Similarly, from the joint family to the Nuclear family to Single Parent! The process on either side is never-ending.
In the late 1990s, the developers of the ISO 9001:2000 standard, which addressed quality management systems and principles debated whether or not to update the use of the word “continuous” to “continual”. ISO Technical Committee 176 and regulatory representatives ultimately decided that “continuous was unenforceable because it meant an organization had to improve minute by minute, whereas, continual improvement meant step-wise improvement or improvement in segments”.
As per ISO 9000: 2015 Standard, clause 3.3.2,
Continual Improvement: Recurring activity to enhance performance
Difference between Continual & Continuous:
As per different dictionaries (Oxford, Merriam-Webster, Cambridge), the definition of Continual and Continuous are quite similar but their intent is different.
Continual: Batch Processing / Periodically Like Quality Month, Improvement plan based on the result of internal or customer audit, Chronic cough
Continuous: Like Single piece flow and improving every day, nonstop (like continuous rain)
The goal of this automotive QMS standard is the development of a quality management system that provides for continual improvement through breakthrough change, innovation and re-organization. The quality policy also includes a commitment to continual improvement of the management system. For any management system to work effectively, it is pertinent to consistently review our existing process and improve it.
The basis for continual improvement project (CIP) is PDCA (Plan, Do, Check, Act). Unless all the steps are followed, the effectiveness of CIP cannot be assured.
Following are the clauses of ISO 9001 and IATF 16949 where the reference of Continual Improvement is specified.
Requirement | Clause |
Goals | Introduction |
General | 0.1 |
Quality Management system & its processes | 4.4.1 |
Quality Policy | 5.2.1 |
Resources | 7.1.1 |
Employee motivation and empowerment | 7.3.2 |
Supplier Development | 8.4.2.5 |
Customer Satisfaction | 9.1.2.1 |
Improvements | 10.1 |
IATF subscribing OEM’s have specified some requirements related to Continual Improvement
BMW, Peugeot, Renault, VW, FCA, Ford | No requirement |
GM | Review of PFMEA annually for critical, safety and high-risk items in manufacturing parts and processes |
As per ISO 9001 & IATF 16949, following are the key points.
Documented Process:
There are 22 mandatory documented processes. Continual improvement is one of them. The organization must define a procedure of how improvement activities will be initiated periodically.
Identify Methodology, Objectives, Measurement, Effectiveness & documented information:
a. In the documented process (procedure), the organization must determine the methodology to identify continual improvements projects across the organization by engaging different stakeholders. It can be the output of management review, internal / customer audit, major rejection etc.
b. Determine tangible and measurable objectives (KPI) so that everyone in the organization is aware, where they are and where they need to reach.
c. On defined periodicity (like a monthly review), measurement of the performance against each KPI needs to be done. It helps to verify the performance of improvement projects.
d. The effectiveness of the continual improvement project needs to be verified by cross-functional team. Management review meeting is one of the platforms for checking the effectiveness.
f. All the KPI, review frequency, performance and its review must be documented so that effectiveness can be monitored and learnings can be utilized for other projects too.
Reduction of Process variation & waste:
Customer does not pay for rejection and waste. One of the key objectives of any continual improvement is to reduce the process variation and waste in the manufacturing process. Some of the key indicators include Inventory Turnover, Cost of poor quality, OEE, Warranty, SPC data, in-process rejection, Scrap, Supplier performance etc.
Risk Analysis:
While implementing any continual improvement project (CIP), it is important to first analyse the possible risk associated with any project. One of the methodologies is to review FMEA (Failure Mode & Effect Analysis) in the beginning and once the project is completed.
Results of analysis and Management Review:
The result of management review output and analysis of data from different processes will be the basis for identification of continual improvement projects. Based on the priority set by management, adequate resources and monitoring mechanism is to be established.
One of the key understanding related to the definition of ‘which projects can be considered as part of continual improvement’ is stated in NOTES of IATF 16949 Clause 10.3.1. It states that “Continual improvement is implemented once manufacturing processes are statistically capable and stable or when product characteristics are predictable and meet customer requirements.”
It means that once the organization has achieved its internal and customer target, the further improvements from their onwards shall be considered as continual improvement. This definition is different from our general understanding, wherein every improvement project is considered as ‘Continual Improvement Project’!
Key Indicators of CIP:
- Internal rejection
- Supplier performance
- Scrap
- Warranty
- OEE
- Inventory turnover
- Customer satisfaction
- Employee Satisfaction
Benefits to Top Management:
- High customer satisfaction
- Reduction in wastages like scrap, rejection, rework
- Improved employee satisfaction
Some question to ponder:
- How often PFMEA is reviewed based on continual improvement projects?
- How many organizations plan continual improvement projects where targets have been met?
- Continual improvement projects are based on PDCA. How many organizations follow all 4 steps?
References:
ISO 9000: 2015
ISO 9001: 2015
IATF 16949: 2016
Customer Specific Requirements (CSR)
This is the 34th article of this Quality Management series. Every weekend, you will find useful information which will make your Management System journey Productive. Please share it with your colleagues too.
Your genuine feedback and response are extremely valuable. Please suggest topics for the coming weeks.
I appreciate it.