FMEA: Difference between Old (4th Edition – 2008) and New Version (1st Edition: 2019 – AIAG/VDA Handbook)
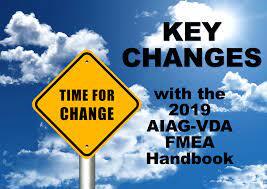
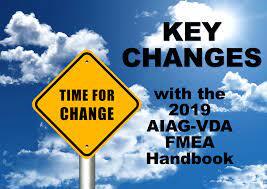
Remember the difference between a boss and a leader; a Boss says “Go!’ a Leader says “Let’s Go!”: E.M. Kelly
Introduction
Across the globe, the generation gap is a common challenge. Each generation thinks that whatever they are doing is right! But who will decide what is right or wrong? I think it depends on the perspective of how we see things. There is some merit in all the generations.
Objective
Failure Mode and Effects Analysis (FMEA) is a well-established method in the manufacturing industry, commonly applied to optimize product/process reliability and cost. It requires cross-functional teams to identify and evaluate the product/process functions, to continuously improve them to reduce risks. The FMEA is a living document and is re-evaluated many times during its lifecycle.
The purpose is to understand the key difference between the old (2008) and the new version so that the new FMEA (Handbook: AIAG & VDA 1st Edition 2019) can be effectively understood and implemented in the organization.
Detailed Information
FMEA (Failure Mode & Effect Analysis) is a team-oriented, systematic, qualitative and analytical method to identify, analyse and mitigate the technical risks related to the ‘product and manufacturing process design.
The FMEA is the ‘Before the Event’ and not the ‘After the Event’ exercise.
The effectiveness of the FMEA can be gauged from the improvement in COQ (Cost of Quality) and COPQ (Cost of Poor Quality)
7 Step Process:
- Planning & Preparation: Objectives, Project identification, plan boundaries
- Structure Analysis: Process Item, Process step, process work element
- Function Analysis: Intended Function/Requirement
- Failure Analysis: Failure Effect, Failure Mode, Failure Cause
- Risk Analysis: Prevention and Detection Control, Severity / Occurrence / Detection
- Optimization: Recommended Actions, Responsibility, target date, revised S, O, D
- Result Documentation
Step 1 (Planning and Preparation)
2019 Version:
- Project plan (5T): InTent, Timing, Team, Task, Tools
Step 2 (Structure Analysis)
2008 Version / 2019 Version:
- Consists of three expanded columns whose purpose is to facilitate a thorough understanding of the process. Start with the Focus Element in the “middle column,” then identify the Process of which the Focus Element is a part and finally identify all Process Work Elements of the Focus Element.
Step 3 (Function Analysis)
2008 Version / 2019 Version:
- Detailed graphical representation of the function (visualization)
- More clarity about the sources of the functional requirements
- Legal Requirements (recycling, environmental)
- Industry norms and Standard (ISO 26262: Functional Safety)
- Customer requirements (drawing, technical specifications)
- Internal requirements (Packaging, Manufacturability)
- Product characteristics (Diameter, surface finish)
Step 4 (Failure Analysis)
2008 Version / 2019 Version:
- Establishment of the failure chain
- Clear linkage between Failure Mode (FM) with Failure Effect (FE) and Failure Cause (FC)
Failure Chain:
- Failure Modes (FM): It means the ways, or modes, in which something might fail.
- Failure Effect (FE): It refers to studying the consequences of those failures’ mode.
- Failure Cause (FC): A indication of why failure mode could occur
Step 5 (Risk Analysis)
2008 Version / 2019 Version:
- Change in the Rating for Severity, Occurrence and Detection for each failure chain
- Evaluation of action priority
Severity (S): Severity of the Failure Effect (FE)
Occurrence (O): Occurrence of the Failure Cause (FC)
Detection (D): Detection of the Failure Cause (FE) and/or Mode (FM)
- The failure effects are given severity rating according to
- End-user- The effect of the process item on to end-user.
- Ship to plant- The effect of the failure mode assuming the defect is not detected before shipping to the next plant
- Your plant- The effect of the failure mode assuming the defect is detected in the plant
Action Priority (AP)
The key objective of ‘Action Priority’ is to choose, how to best prioritize the efforts to reduce the risk.
Priority High (H):
- Highest priority for review and action.
- Either identify an appropriate action to improve prevention and/or detection
- Or justify and document why current controls are adequate
Priority Medium (M):
- Medium priority for review and action.
- Either identify an appropriate action to improve prevention and/or detection
- Or at the discretion of the organization, justify and document why controls are adequate
Priority Low (L):
- Low priority for review and action.
- Could identify actions to improve prevention or detection controls
Step 6 (Optimization)
2008 Version / 2019 Version:
- Separate Prevention and detection controls
References:
IATF 16949: 2016
FMEA Handbook (AIAG-VDA 1st Edition June 2019)
FMEA 4th Edition 2008
Industry Experts
This is the 130th article of this Quality Management series. Every weekend, you will find useful information that will make your Management System journey Productive. Please share it with your colleagues too.
In the words of Albert Einstein, “The important thing is never to stop questioning.” I invite you to ask anything about the above subject. Questions and answers are the lifeblood of learning, and we are all learning. I will answer all questions to the best of my ability and promise to keep personal information confidential.
Your genuine feedback and response are extremely valuable. Please suggest topics for the coming weeks.
Hello, thanks for explanation, do you have a template for DFMEA and PFMEA which you can easely share?
Dear Denis, Thanks for your response. The template can be retrieved from Google. I do not have it.
Really an excellent explanation. Thank you very much!!!
Dear Mr Padmanabhan, Thanks for going through the blog and sharing your kind thoughts.