What is the key difference between Employee / Customer / Onsite supplier- owned equipment?
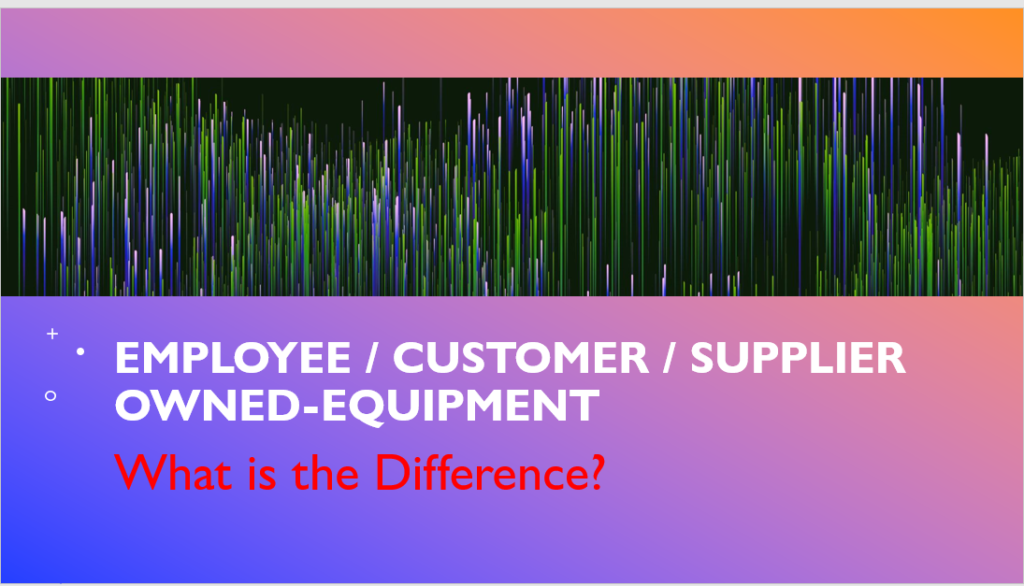
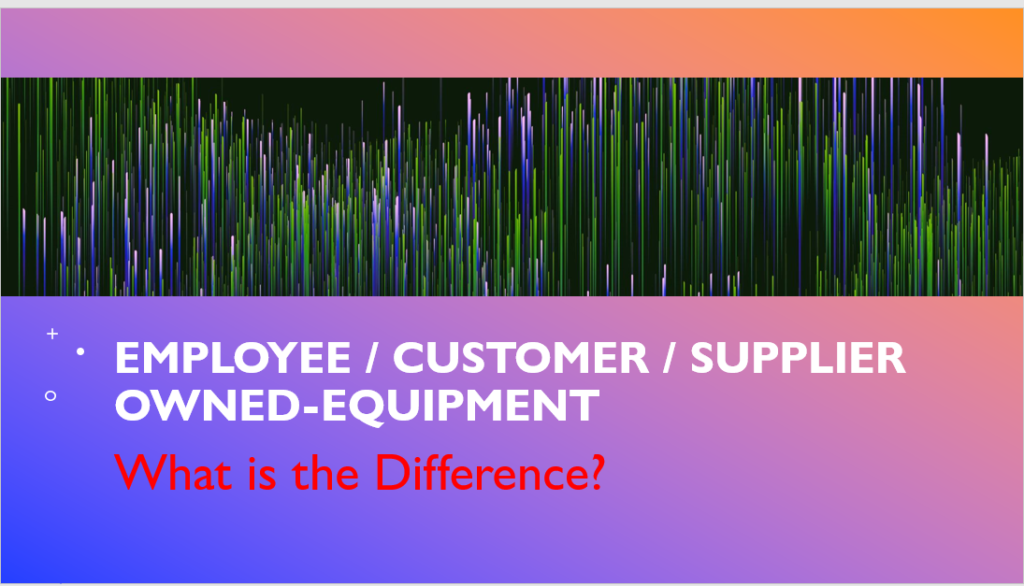
The difference between the impossible and the possible lies in a man’s determination: Tommy Lasorda
Introduction
We are only concerned about our wellbeing, which generally includes our immediate family. At times, we fail to recognize that there are many important stakeholders which are equally crucial for our happiness like maids, security guards, vendors etc. Without them, our routine life is incomplete and strenuous. Once we start considering these associates as an important part of our ecosystem, we can create a win-win situation for everyone.
Objective
While calibrating/verifying the gauges, measuring instruments and test equipment, the organization should consider all kinds of instruments like Employee-owned / Customer-owned / Onsite supplier owned equipment. The intent is ensuring that while calibrating/verifying, the organization should not only consider those instruments which are owned and managed by the organization but also those owned by employee/customer/supplier. The quality of the product and process control hinges on all of them.
Definitions: ISO 9000: 2015
Verification (Cl 3.8.12): Confirmation through the provision of objective evidence that specified requirements have been fulfilled.
Calibration: It is the process of comparing an unknown quantity or value to a known quantity. A trained calibration technician will check the instrument at several points through its range and may make adjustments to align the instrument with the standard if it is found to be out of tolerance.
Detailed Information
Any instruments that are used to assess conformance to requirements, regardless of who owns them, need to be in the calibration program. they’ll need some identification method too.
As per Clause 7.1.5.2.1 of ISO 9001 and IATF 16949, apart from organization owned instruments, the organization should also consider the organization Employee-owned / Customer-owned / Onsite supplier owned equipment.
Employee-owned: The measuring instruments are either purchased by the employee or given by the organization to the employee for inspection/testing.
Customer-owned: The measuring instruments are purchased by the customer and are given to the organization for inspection/testing.
Onsite Supplier owned: The measuring instruments are either purchased on lease or outsourced by the supplier to the organization for inspection/testing.
Where Calibration of Employee/Customer/Onsite supplier owned equipment is needed?
- If the measurement equipment affects the quality of the final product
- If there is a customer requirement
- If there is a legislative and regulatory requirement
- If it is organizations internal requirement
Possible RISK with Employee/Customer/Supplier owned instruments:
- Risk of producing a nonconforming product
- Employee may not be interested to pay the cost of calibration
- The organization may not be interested to pay calibration cost for the employee-owned instruments
- The organization does not consider these instruments for calibration/verification
- Customer/Supplier does not feel the importance to verify whether their supplied instruments are calibrated/verified
Key difference between Employee / Customer / Onsite Supplier owned equipment:
S.No. | Employee Owned | Customer Owned | Supplier Owned |
1 | Employee-owned equipment must be approved for use before using it for inspection to ensure it is of sufficient quality to do the job right | Provided by the customer for inspection or testing | Due to high cost, instead of purchasing, the supplier installs their test equipment at the organization end and charge a commission |
2 | Their gauges need to be part of the overall calibration plan | Same measuring equipment is also kept at the customer end for re-verifying the results | The measuring and test equipment should be calibrated/verified |
3 | Use these gauges just to monitor for problems | Sometimes shared by the customer when an organization does not have the competence to manufacture it | Example: CMM or Salt spray test hired and managed by the supplier |
4 | If not calibrated, identified as “reference only” gauges | Sometimes shared by the customer so that quality of the product despatched to the customer can be ensured | Many times, suppliers conduct some value addition like assembly, testing etc. at their customer end |
5 | Periodically monitor how the tools affect the process | Example: Final fitment gauge | The measuring and test equipment used at the customer end should be considered for calibration/verification |
6 | Either cost of the calibration can be paid by the company or employee else, the gauge has to be removed | ||
7 | Used in some parts of USA, Mexico, Europe and Japan |
Present Challenges:
- Very often the organization fail to consider the measuring instruments provided by customer or supplier for calibration/verification
- The master list of instruments does not include a list of measuring instruments, gauges and test equipment provided by customer or supplier.
- How often the responsible person reviews the report received from the calibration agency for its adequacy?
References:
ISO 9000: 2015
ISO 9001: 2015
IATF 16949: 2016
ISO 10012: 2003
ISO 17025: 2017
Industry Experts
This is the 103rd article of this Quality Management series. Every weekend, you will find useful information that will make your Management System journey Productive. Please share it with your colleagues too.
Your genuine feedback and response are extremely valuable. Please suggest topics for the coming weeks.
Recent Comments