Problem Solving Technique: Step 6- Horizontal Deployment (Corrective Action)
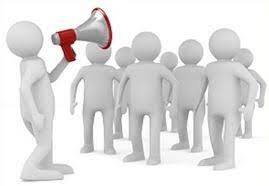
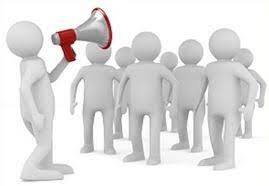
“ There is no joy in possession without sharing.” — Erasmus
Introduction
Referral plays a very important role in our lives. For any marriage function, we prefer to give work to a food caterer who had already provided similar service to our family and friend. When we buy a car and we are satisfied with the feature and performance, we share our experience with our dear ones.
Objective
The purpose of a quality management system is to help businesses improve their abilities to consistently meet customer or regulatory requirements. A major component of a successful system is a corrective action program that adequately addresses nonconformances. Quality pioneer W. Edwards Deming introduced the Plan-Do-Study-Act (PDSA) cycle as a planning, implementation, and continuous improvement tool.
In the problem-solving technique (like 8D Model), one of the pertinent steps is to implement horizontal deployment. It should be implemented once the actions are effectively implemented in one process and the results are consistent. Without effective implementation and consistent results, horizontal deployment should be avoided.
Definitions (ISO 9000: 2015):
Complaint (clause 3.9.3): Expression of dissatisfaction made to an organization related to its product or service or the complaints handling process itself where a response or resolution is explicitly or implicitly expected.
Corrective Action (Cl 3.12.2): Action to eliminate the cause of nonconformity and to prevent reoccurrence.
Correction (Cl 3.12.3): Action to eliminate a detected nonconformity
Complainant (clause 3.1; ISO 10001: 2018): Person, organization or their representative making a complaint.
Read More: https://bit.ly/Step1DefineProblem
Detailed Information:
The following are the 7 key steps for problem-solving.
- Define the Problem
- Correction, Containment, Interim Action
- Root Cause Analysis: 3 Layered 5 Why Analysis (3L5Y), Ishikawa Diagram
- Implementation of Corrective Action
- Effectiveness Evaluation
- Horizontal Deployment (Yokoten: Japanese)
- Documentation, Lesson Learned and Promotion of Awareness
Read More: https://bit.ly/ProblemSolvingTechnique
As per the PDCA cycle, once the organization implement the Correction and Corrective Actions (Do), verified their effectiveness (Check), the last logical step is to implement similar actions on similar kind of product and processes so that related type of problems can be averted before they occur.
Purpose of Horizontal deployment:
The horizontal deployment (Yokoten) is not only about the best results and successes. It’s crucial that this sharing and peer-to-peer learning includes both successes and failures. The formal practice of sharing the learning from failure makes it less likely we hide failures.
At Toyota, the expectation is that improvement is not complete until horizontal deployment (Yokoten) is confirmed and the learning is shared with others. It is part of the culture. Horizontal deployment is not only to copy the superficial best practice process but also to understand the underlying assumptions and background conditions for success. Just as Toyota has learned, it is not enough to copy the result of good improvement (kaizen), we must also copy the thinking that resulted in the improvement.
In a typical company, the best practices can become lost among the noise, buried beneath the day-to-day firefighting or even deliberately hidden from others to make oneself or the group look good. There may be localized incentives in place that prevent horizontal deployment from happening. There are other obstacles, including a lack of documented standard, weak “go see” culture, or no metrics or ways to agree on what is a better practice.
Read More: https://bit.ly/CorrectionContainmentInterim
How to implement Horizontal Deployment:
Systemic:
Based on the systemic analysis, the root cause is identified and actions are implemented but whether all the other possible failures are considered or not (Example: Root cause for the relay failure was dust and some actions are planned but dust can also impact other electronic components like semiconductor, resistor, capacitor etc. Have we deployed horizontal actions for other possible failures too?)
Man:
On the job training provided to the operator in one final inspection line can be duplicated for remaining lines too (Example: QR Code wrongly identified in the final packing)
Read More: https://bit.ly/RootCauseAnalysis3L5Y
Machine:
- Safety features are provided on the fabrication machine so that operator safety can be ensured during the production process. The same safety feature can be implemented on identical machines too (Example: Two hand Control Switches on the fabrication machines)
- Fixture implemented in one machine can be implemented in other machines too where similar kind of problem can come (Example: PP moulding – Cooling Fixture)
- Poka-Yoke implemented at one manufacturing process can be duplicated in other processes (Example: Spring missing)
Material:
To fulfill the End of the Life (EOL) requirement, action implemented on one type of material can be implemented on other variants too (Example: Lead-Free Wiring harness for all types of electrical fitting)
Read More: https://bit.ly/IshikawaDiagram
Method:
For the synchronous flow of the material, the process flow can be reviewed and changed for one product line. Similar process flow can be implemented for other product lines too (Example: In-process material is going out of the factory for outsourcing process 2 times (Painting and Sandblasting. The sequence can be changed so that both the processes can happen together).
- Special characteristics identified in one process can be also identified in similar processes (Example: Torque testing in one assembly line is identified as a special characteristic, the similar kind of torquing which can impact the final product can also be identified as a special characteristic)
Read More: https://bit.ly/CorrectiveActionStep5
Possible Benefits:
- Upcoming problems/defects can be averted
- Repeated customer complaints/Internal issues can be minimized
- Cost of Poor Quality (COPQ) will be reduced
- Employee and Customer satisfaction will enhance
Read More: https://bit.ly/Step5EffectivenessImplementation
Industry Challenges:
- How often do organizations have a process of deploying the learnings from one process in other processes too?
- How often do the organizations first verify the effectiveness of the action plan at one process/product before deploying it on the related processes/products?
- How often do organizations have a process of verifying the effectiveness of horizontal deployment?
References:
IATF 16949: 2016
ISO 9001: 2015
ISO 9000: 2015
OEM Supplier Manual
CQI 20: Aug 2018, 2nd Edition (Effective Problem-Solving Guide)
Industry Experts
This is the 147th article of this Quality Management series. Every weekend, you will find useful information that will make your Management System journey Productive. Please share it with your colleagues too.
In the words of Albert Einstein, “The important thing is never to stop questioning.” I invite you to ask anything about the above subject. Questions and answers are the lifeblood of learning, and we are all learning. I will answer all questions to the best of my ability and promise to keep personal information confidential.
Your genuine feedback and response are extremely valuable. Please suggest topics for the coming weeks.
Recent Comments