Maintenance Process: Challenges & Resolution
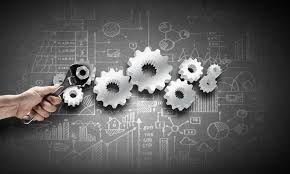
Maintenance Process: Challenges & Resolution
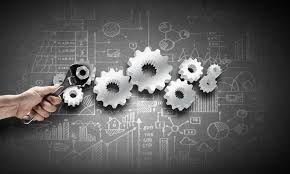
“Obstacles are challenges for the winner and excuses are for the losers”: Marijane Meaker
After conquering the Mount Everest by Edmund Hillary & Tenzing Norgay on May 29, 1953, Hillary said ‘it is not the mountain that we conquer, but ourselves.’ The challenges are always more internal than external. As we get more clarity about our internal self, either the problems disappear or their size reduces.
In the industrial environment too, in general, organizations are aware of the challenges that they are facing and possible solutions too. But the real question is when they want to accept and see it.
For maintenance process also, the process owners are aware of the problems related to machine efficiency and quality of the products but they seek external help to solve their problems (like TPM methodology). But the success and sustenance of any methodology will depend upon the conviction & commitment of the process owners to improve.
Following are some of the common problems that maintenance process faces, its impact on the product and process, what can be the possible reasons and possible measures.
S.No. | (1) Possible Challenges | (2) Impact
(related to 1) |
(3) Possible Reasons
(related to 1) |
(4) Possible Measures
(related to 3) |
1 | Inadequate competence of the operator running the machine
|
–Improper w
ay of running the machine -Frequent breakdown of the machine -Loss of productivity |
Competency not defined
|
Competency of the operator as per type and criticality of the machine can be defined
|
Non-availability of a qualified operator
|
–Multiskilling can be done.
–On-job training can be provided before handing over the machine independently |
|||
Competency of the operator is not considered important | –Data for machine breakdown and rejection due to the operator can be analysed to understand the gravity of the issue | |||
2 | Not effectively implementing ‘My Machine’ concept (even in many TPM awarded companies)
|
–Dependency on the maintenance team will continue
-The maintenance team will be more focused on routine work rather than improvements
|
Focus on production numbers only | –Benefits of ‘my machine’ concept can be understood again.
–Data on productivity and quality loss attributed to the behaviour of the operator can be analysed to understand the importance of ‘my machine’ concept |
Frequent changeover of the operator (temporary/contract) | –Multiskilling
–Additional pool of operator who can quickly learn and replace –The incentive to operator valuing the concept of ‘my machine’. |
|||
3 | Not getting a machine on time (as per schedule) for preventive maintenance
|
-Frequent breakdown & OEE target not achieved
-Possibility of accident increases -The additional load on maintenance personnel to work on the weekend and break time like lunch etc. |
Too much focus on achieving production target (numbers) | -Trend analysis of data for the last few years can give a clear idea about frequent and long breakdown time and its impact on productivity, quality, cost and health
-Employee satisfaction survey of maintenance personnel |
Low importance of preventive maintenance | ||||
4 | At the design stage, improper selection of machine
|
-Voice of customer related to Productivity and Quality target will not be met
-Production team always struggle -The maintenance team will always be on toes to keep the machine in working condition |
Not understanding the expectation of customer and its linkage with appropriate selection of machine | -Involve all relevant person during the initial technical review with the customer
-Provide training and enhance competence where needed |
Costing not done correctly leading to pressure on procuring incapable/low-cost machines | -Involving a competent person for feasibility & costing
-Review TGW (Things Going Wrong) from previous projects |
|||
Not involving relevant personnel for selection of machine during the process design phase | Involving relevant process owner during initial feasibility, costing and process design phase | |||
5 | Poor quality of critical spare parts due to budgetary constraint
|
-Frequent machine breakdown
-Productivity & quality loss -Possibility of accident
|
-Not involving a relevant person to select the spare parts | Involve the relevant and competent person |
-More focus on costing saving | Analyze cost (direct & indirect) saved by using inferior quality and reduction in OEE% | |||
–Not understanding the impact of poor quality of spare parts on the process | –Voice of process owner should be given importance.
–Relevant CFT can decide rather than one individual |
|||
6 | Due to production pressure, too much utilization of machine (break time, weekend, maintenance time)
|
-Frequent breakdown
-Reduced life of the machine -Early depreciation of the machine –The health of the machine and operator will deteriorate fast |
No capacity calculation or its review and up-dating | –Correct calculation of plant capacity and sharing with top management for further decision |
Variation in customer schedule | Can review the trend for the last few years and build up inventory accordingly | |||
Poor planning | -Provide training
-Recruit competent persons -Periodic review of the performance by top management |
|||
7 | Non-involvement of top management
|
-Other process owner does not consider maintenance process seriously
-Deterioration continues till the customer schedules get impacted and the cost of production increases |
Not an important process which may be directly impacting the profitability and customer satisfaction | MIS can specify indirect losses for productivity, quality and cost due to poor maintenance of machines |
8 | Preventive and predictive maintenance on paper!
|
-Deterioration of the machines
-Low confidence in the maintenance process
|
No monitoring of their process | Periodic review of key indicators like OEE, MTBF, MTTR, MMTM, MTBM |
Low confidence in the maintenance process for improving profitability and product quality | Impact on the bottom line (profitability) due to poor OEE and product quality can be reviewed due to poor maintenance | |||
9 | Inaccurate reporting of Maintenance KPI like breakdown hours
|
-The real situation is never understood
-Machine availability will always be low -Production will always struggle to meet the target |
-Fear of showing real data to management
-No one is verifying the authenticity of the data |
-Analysing the maintenance data in linkage with KPI of production and quality
-Take suitable action, where needed |
-To get appreciation from management and other relevant agencies related to awards! | ||||
10 | Non-replacement of ageing equipment
|
-Frequent breakdown of machines
-Unpredictable machine behaviour -Productivity and quality loss |
-Lack of focus of top management | -Work on regular preventive and predictive maintenance
-Review the losses due to machines |
-No machine duplication plan | ||||
-The poor financial situation of the organization |
There are many more challenges related to the maintenance process which industry is aware of.
Possible Benefits:
- Improved productivity
- Zero Breakdown
- Zero Accident
- Zero defect
- Improved OEE%
- Improved employee morale
- Improved customer satisfaction
References:
IATF 16949: 2016
ISO 9001: 2015
This is the 73rd article of this Quality Management series. Every weekend, you will find useful information that will make your Management System journey Productive. Please share it with your colleagues too.
Your genuine feedback and response are extremely valuable. Please suggest topics for the coming weeks.
The lectures are very helpful both for me and also for the organisation as a whole
Nice write up on maintenance with in-depth knowledge
Thanks Mr Juneja.
Thanks Devraj. Please suggest, how it can be improved.