What is the key difference between Preventive and Predictive Maintenance?
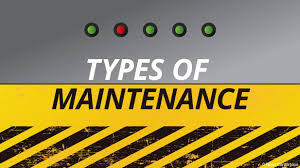
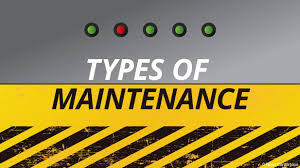
To be happy in life you must learn the difference between what you want vs need: Unknown
Introduction
It is said that ‘prevention is better than cure.’ In the present times of COVID, we can prevent it by wearing a mask, keeping a proper distance, and avoiding unnecessary movement.
Someone has also said, ‘prediction is very difficult, especially if it is about the future.’ Human beings are generally curious to know about the future so that they can prepare themselves accordingly, especially if it is not favorable. Soothsayers (fortune-teller) predicts our future, marriage dates, and even the results of the Football World cup!
Objective
Maintenance is an integral component of operating manufacturing equipment. Preventive or Predictive maintenance are two keys ways of conducting industrial maintenance. Both are vastly superior to the third alternative — reactive maintenance, which essentially is addressing machinery only after it breaks down.
By understanding the key differences between the two, the organization can effectively implement them as per their requirement and control the objectives like OEE (Overall Equipment Effectiveness, MTTR (Mean Time To Repair), MTBF (Mean Time Between Failure), MTTM (Mean Time To Maintenance), etc.
Definitions
Total Productive Maintenance: A system of maintaining and improving the integrity of production and quality systems through machines, equipment, processes, and employees that add value to the organization.
Predictive Maintenance: An approach and set of techniques to evaluate the condition of in-service equipment by performing periodic or continuous monitoring of equipment conditions, in order to predict when maintenance should be performed
Preventive Maintenance: Planned activities at regular intervals (time-based, Periodic inspection, and overhaul) to eliminate causes of equipment failure and unscheduled interruptions to production, as an output of the Manufacturing process design
Detailed Information
If you want to lead an effective equipment management strategy, you can’t afford to rely solely on reactive maintenance. The most cost-effective strategies take a proactive approach to assets conservation, which includes both predictive and preventive maintenance work.
These two maintenance methods aim to increase the reliability of equipment and reduce the likelihood of machine failure, consequently, reducing the high costs of unplanned maintenance. Although they have the same goal and are complementary to each other, still preventive and predictive maintenance are not the same.
Preventive Maintenance: It is a type of maintenance performed cyclically on pre-determined equipment to optimize their working conditions.
Its key purpose:
- To extend the useful life of an asset
- Prevent breakdowns from occurring
- Make repeated breakdown as zero
- To ensure the predictability of the equipment
- To increase MTBF (Mean Time Between Failure)
- Reduction of MTBM (Mean Time Between Maintenance)
- Reduction of MTTM (Mean Time To Maintain)
Predictive Maintenance: Its goal is to catch potential equipment malfunction as early as possible to avoid the need for bigger maintenance activities.
Its key purpose:
- To improve Return on Investment (ROI)
- Reduction in maintenance costs
- Elimination of sudden breakdowns
- Reduction in downtime
- Increase in production performance
From the perspective of the manufacturing industry, the following are some of the key differences between Preventive and Predictive Maintenance:
S.No. | Preventive Maintenance | Predictive Maintenance |
1 | to extend the useful life of an asset | Failure diagnosis by defining the specific problem. Its objective is to estimate how much longer could operate the machine without the risk of sudden failure |
2 | to ensure the predictability of the equipment | predictions are based on the condition of the equipment that is evaluated based on the data gathered through the use of various condition monitoring sensors and techniques |
3 | can be performed after stopping the machine from normal production mode | can be performed as the machines are running in their normal production modes |
4 | is planned at regular intervals | is proactive approach |
5 | occurs on the same schedule every cycle | occurs as needed, drawing on real-time collection and analysis of machine operation data |
6 | means fixing small problems before they become big ones! | predict when equipment might fail so that maintenance work can be performed just before that happens. |
7 | costs of performing preventive maintenance should always be less than the cost of failure. | can provide an ROI that turns the maintenance department into a source of cost-savings and higher profits
|
8 | based on the recommendation of the machine manufacturer and best practices | based on the actual condition of the equipment and its current condition |
9 | is designed to keep parts in good repair | based on the data, even if a shutdown is required, it will be shorter and more targeted. |
10 | often consists of a checklist | Relies on interconnected measurement and data collection systems as well as tools and personnel to analyze that data |
Present Challenges
- How often preventive and predictive maintenance is actually conducted and not on paper?
- How often top management is interested in knowing the effectiveness of preventive and predictive maintenance processes?
- How often maintenance personnel are competent enough to understand the entire checklist (electrical, electronic, pneumatic, hydraulic, and mechanical) and conduct PM accordingly?
References:
IATF 16949: 2016
Industry Experts
This is the 118th article of this Quality Management series. Every weekend, you will find useful information that will make your Management System journey Productive. Please share it with your colleagues too.
Your genuine feedback and response are extremely valuable. Please suggest topics for the coming weeks.
Recent Comments